Surface Finishing Services
- High-quality finishes boost aesthetics and functionality, regardless of the manufacturing method
- Our expert finishing brings your metal, composite, or plastic parts to life
- Fast, precise finishing ensures parts meet specs and speeds up your timeline
Capabilities for Our Surface Finishing Services
Our surface finishing services offer comprehensive solutions for better products’ performance, and appearance. Here’s what you can expect:
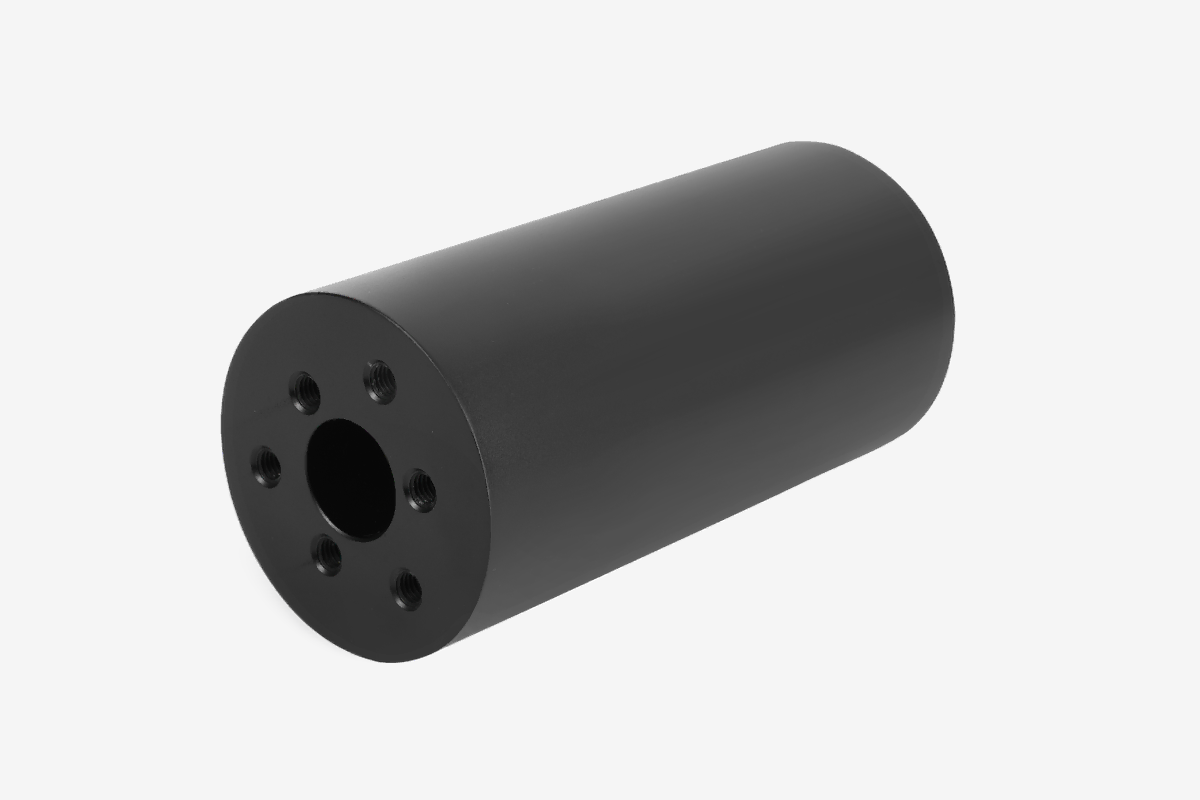
Anodizing
Anodizing is an electrochemical process that creates a oxide layer providing strength, hardness, and corrosion resistance, and color options for your metal parts
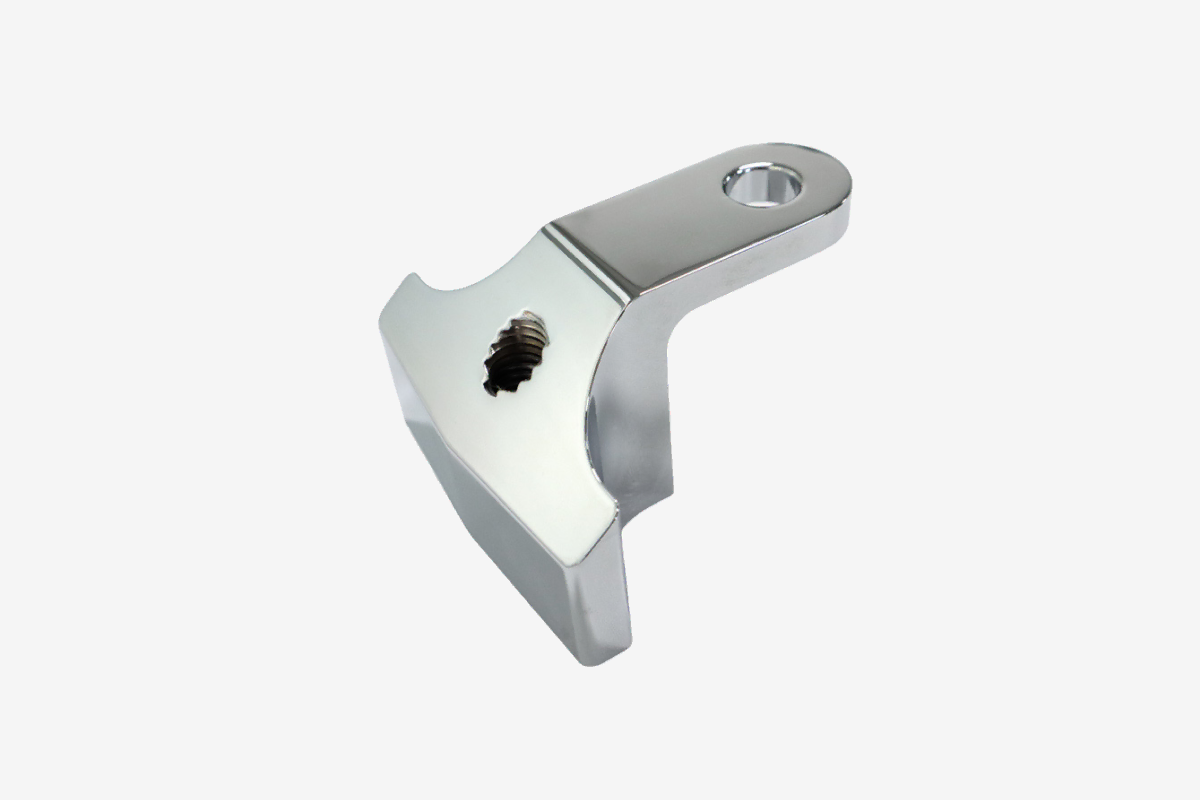
Electroplating
Electroplating involves the electrolytic addition of a thin layer of metal on a workpiece for better functional or aesthetics attributes.
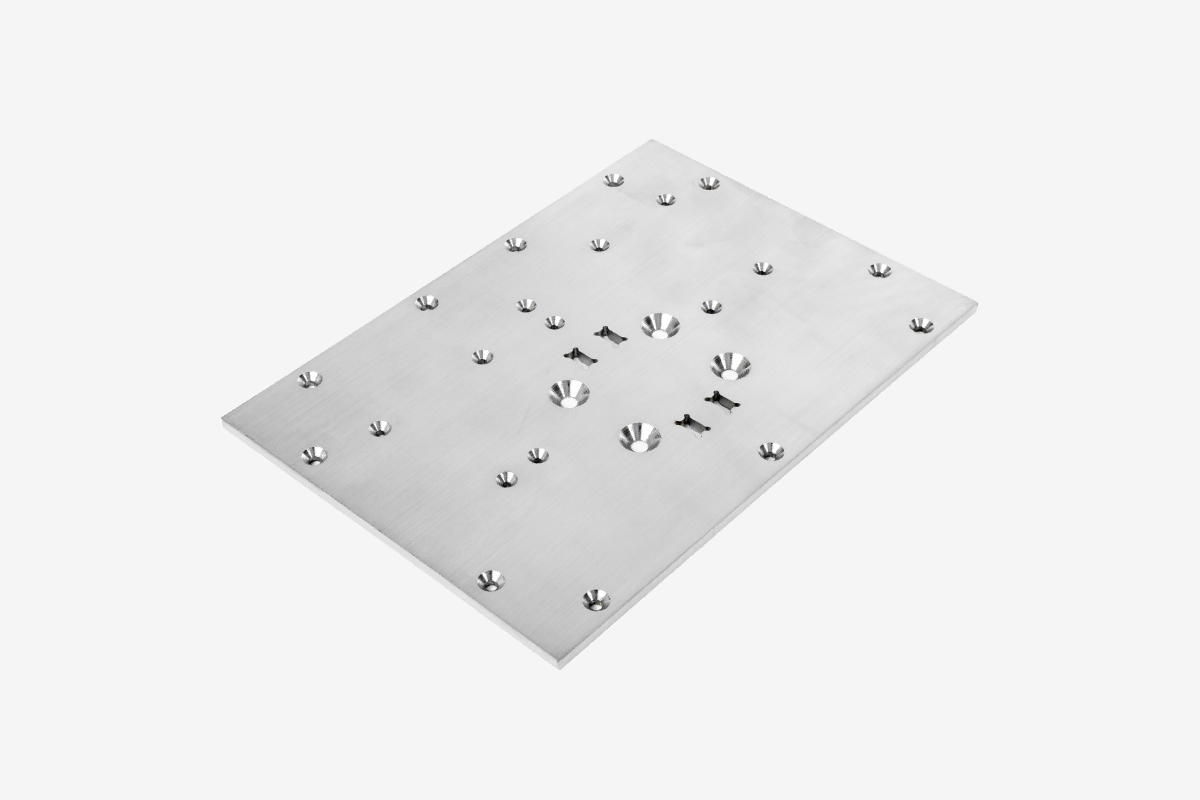
Polishing
Polishing involves using an abrasive material to create a shiny, mirror-like finish on metals like steel and aluminum
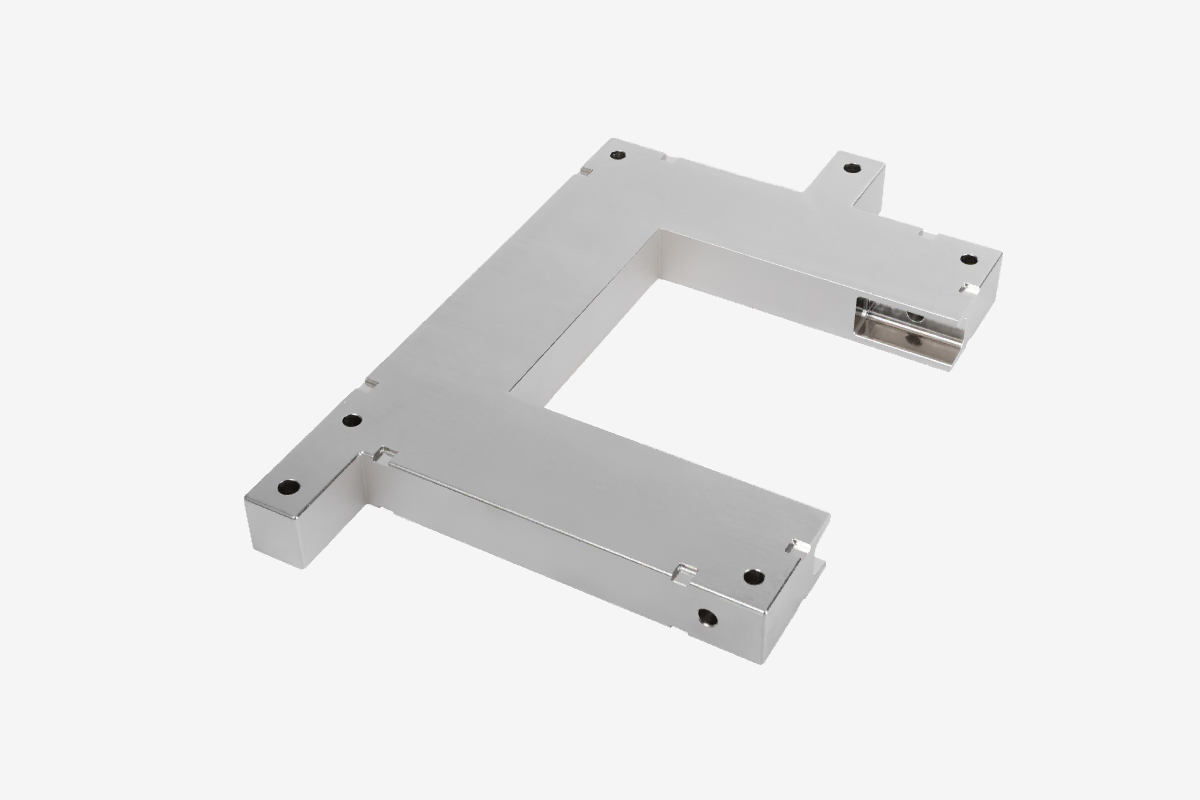
Plating
Plating involves adding a layer of metal like zinc, chrome, or copper, on a workpiece for better functionality such as corrosion resistance and aesthetics due to the numerous color option.
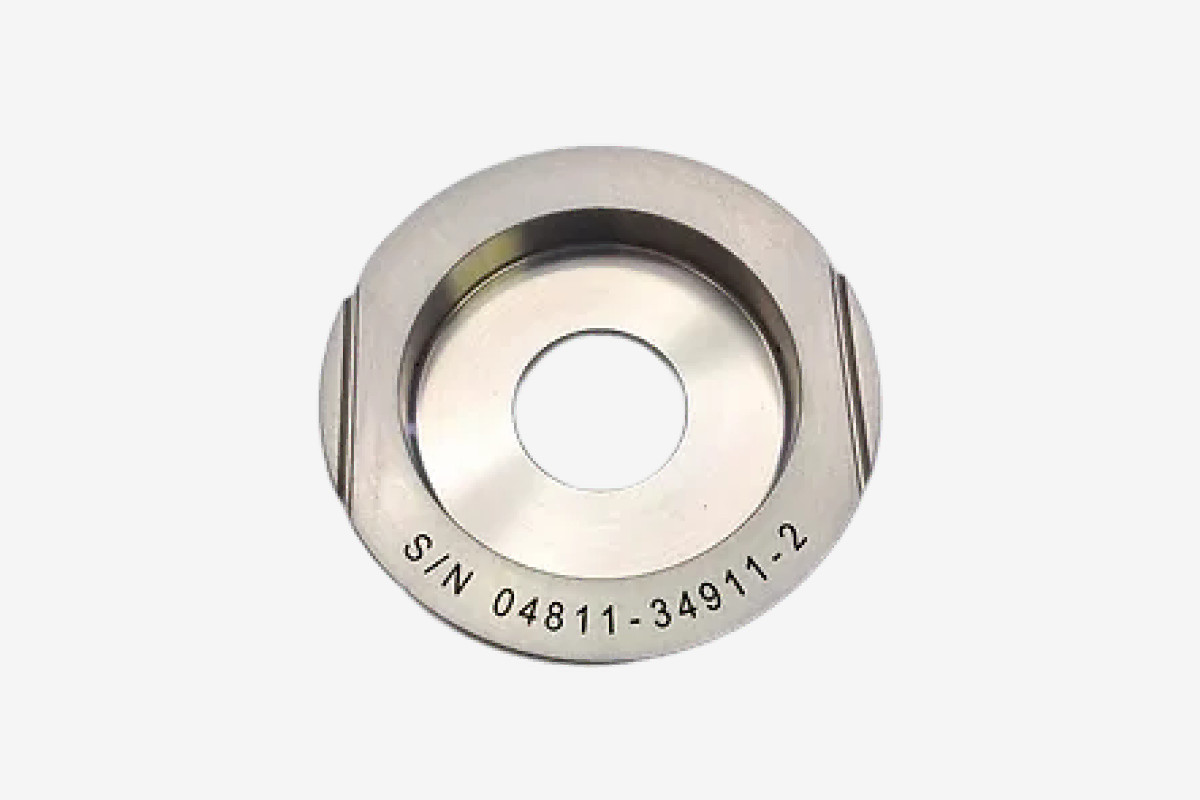
Laser Etching
Laser etching is a marking system that creates permanent marks on metals or plastics by using laser beam to raise the surface of the materials.

Heat Treatment
Heat treatment involves heating a metal to a specific temperature to boost its strength, hardness, and wear resistance, improving performance in harsh environments

Black Oxide
Black oxide is a chemical conversion coating for ferrous materials that creates a black finish on parts providing corrosion resistance without dimensional changes.
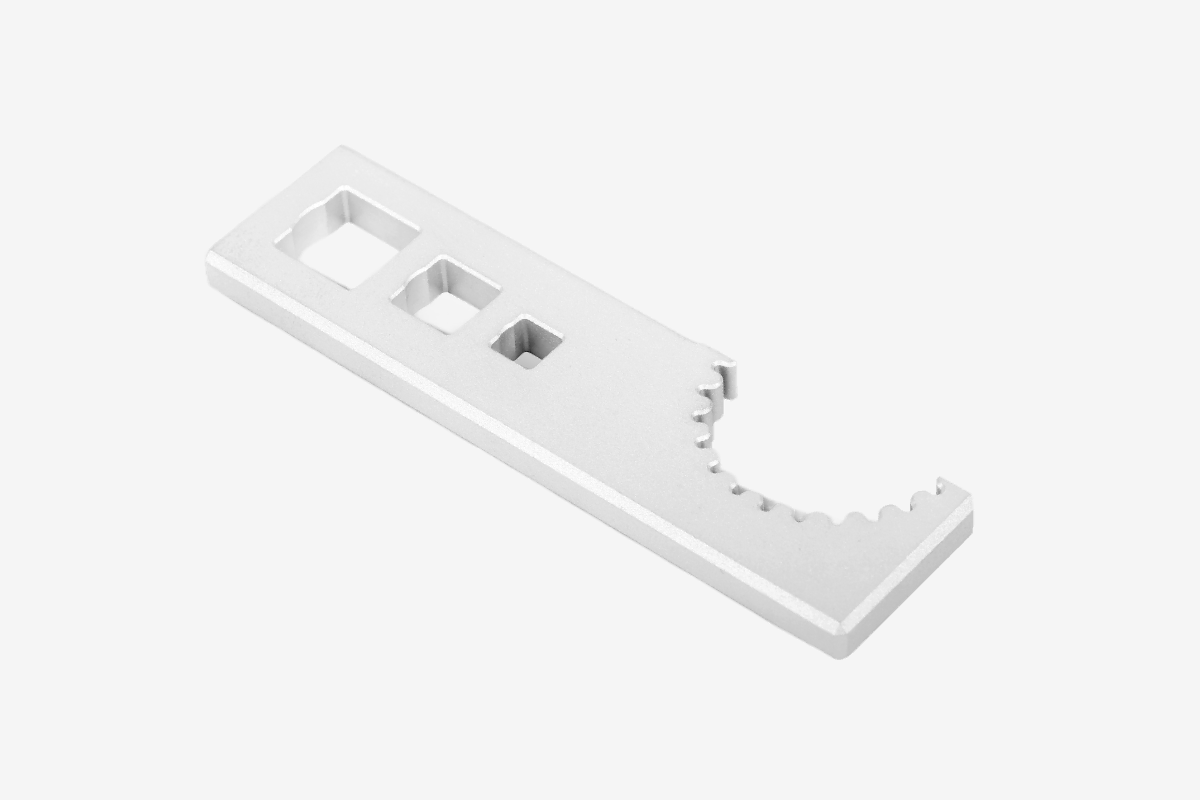
Painting
Our industrial painting services uses advanced coating materials and a well-curated painting process to improve functions and aesthetics.
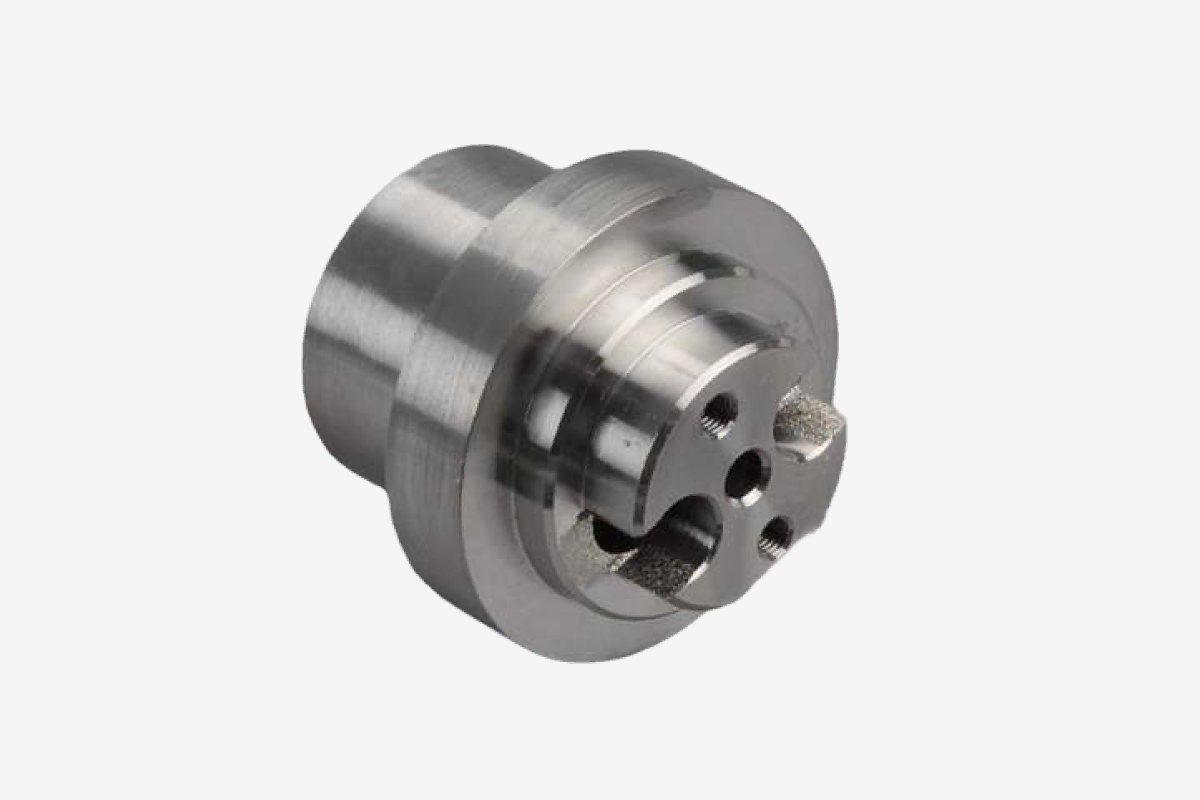
Passivation
Passivation cleans stainless steel, adding a protective oxide layer for better corrosion resistance and durability in tough environments.
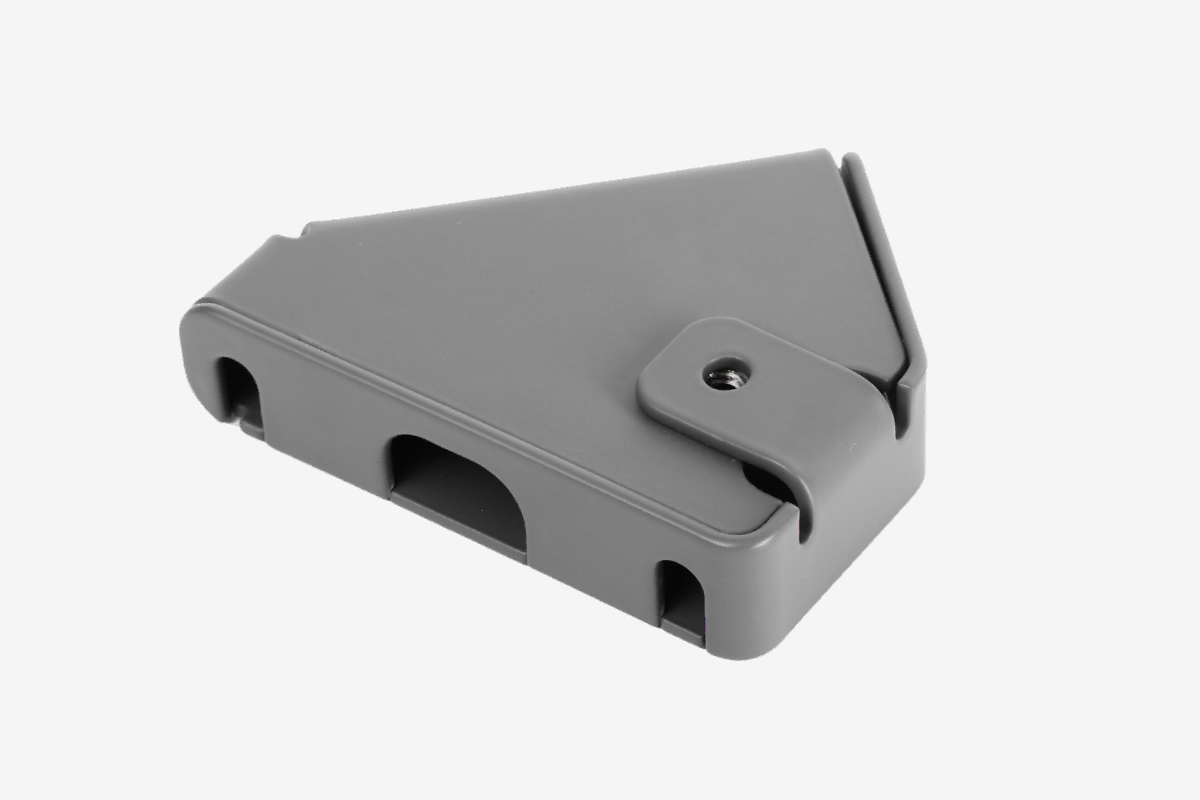
Powder Coating
Powder coating applies a tough, wear-resistant finish to parts, ideal for outdoor gear and machinery. It comes in various colors and offers excellent protection.
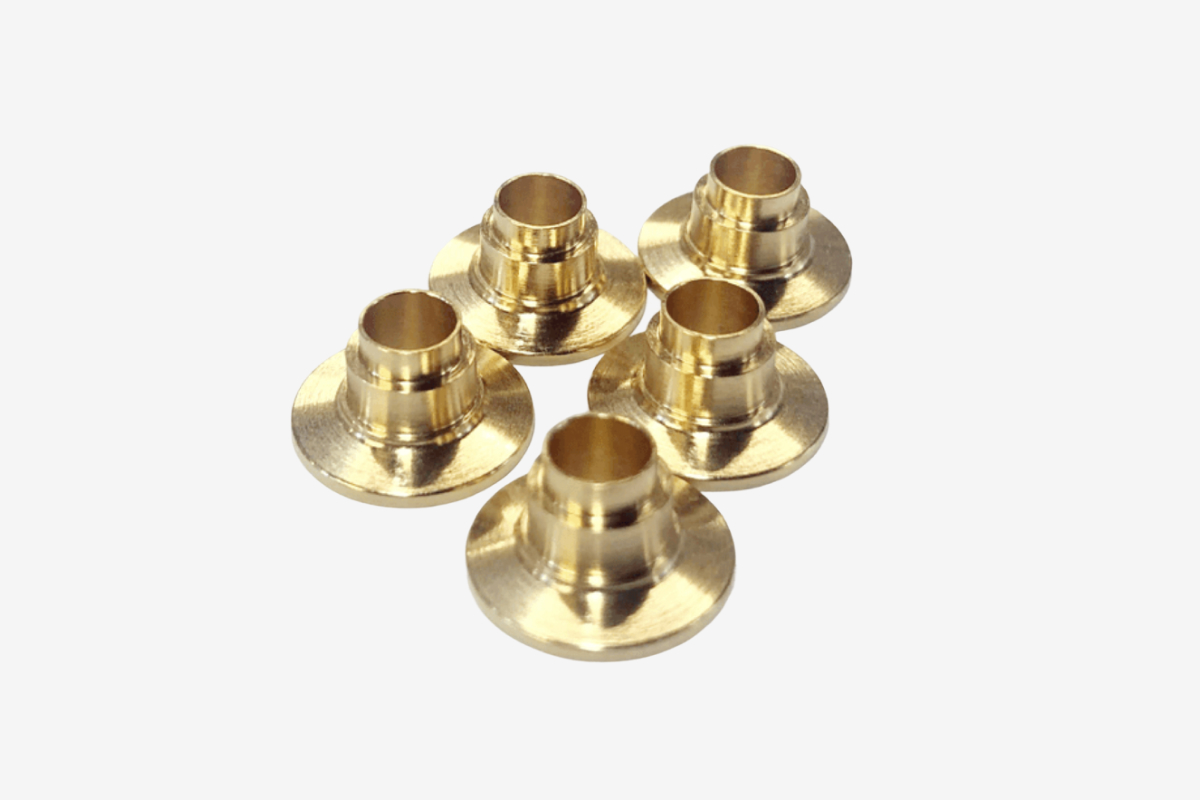
Gold Plating
Enhances conductivity, corrosion resistance, and aesthetics, commonly used in electronics and luxury items.
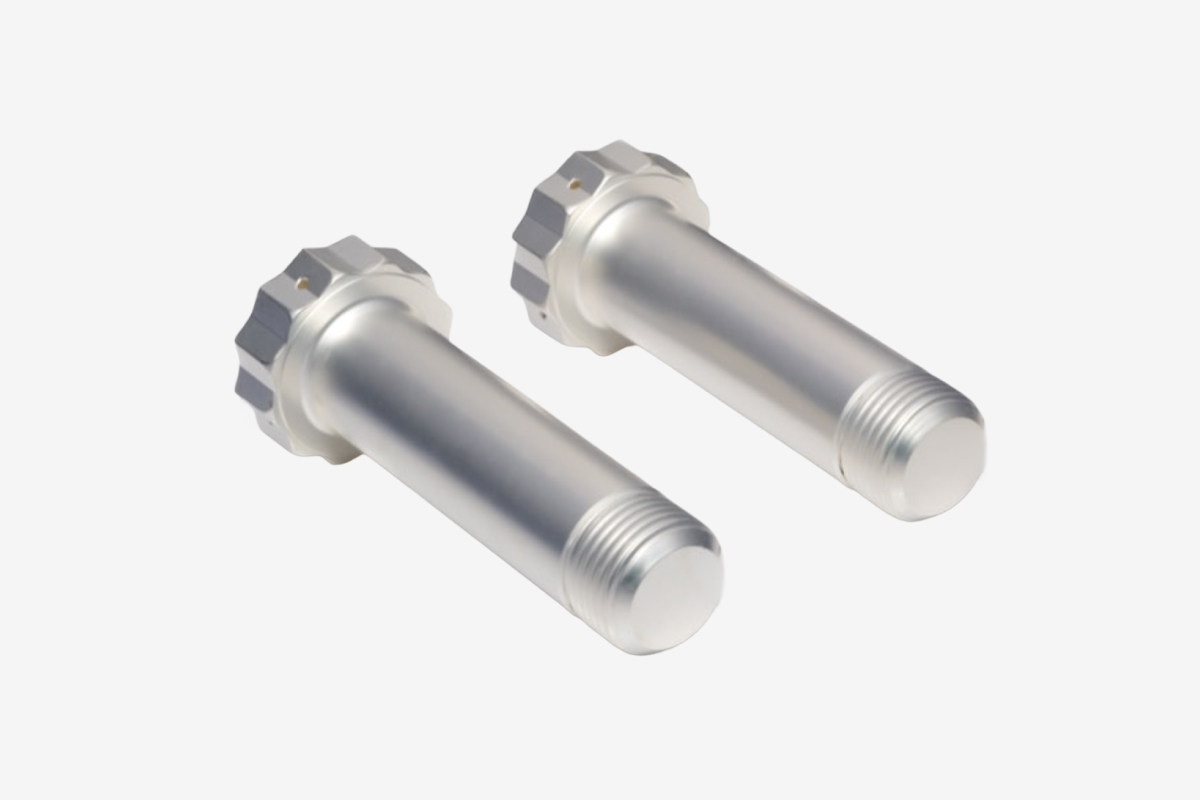
Silver Plating
Provides high conductivity and antibacterial properties, ideal for electrical and medical applications.
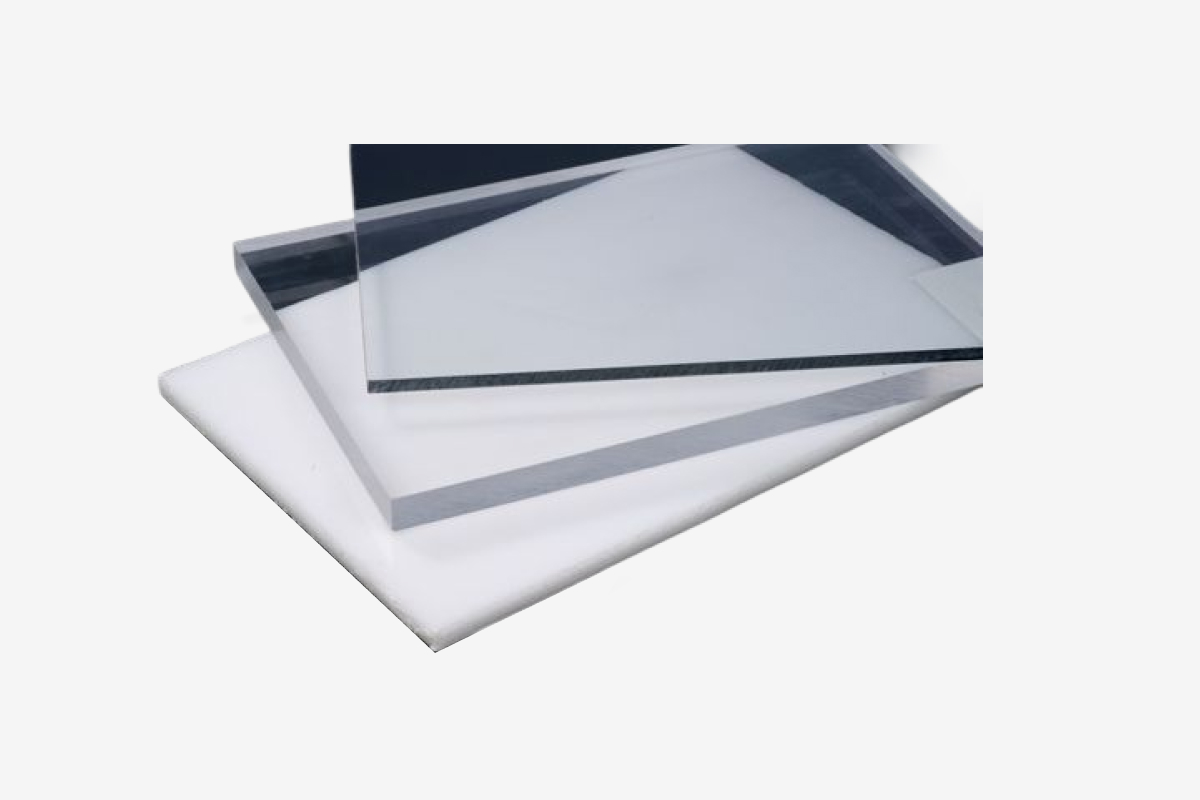
Fumigation Transparent Coating
A protective transparent layer to enhance durability and surface clarity.
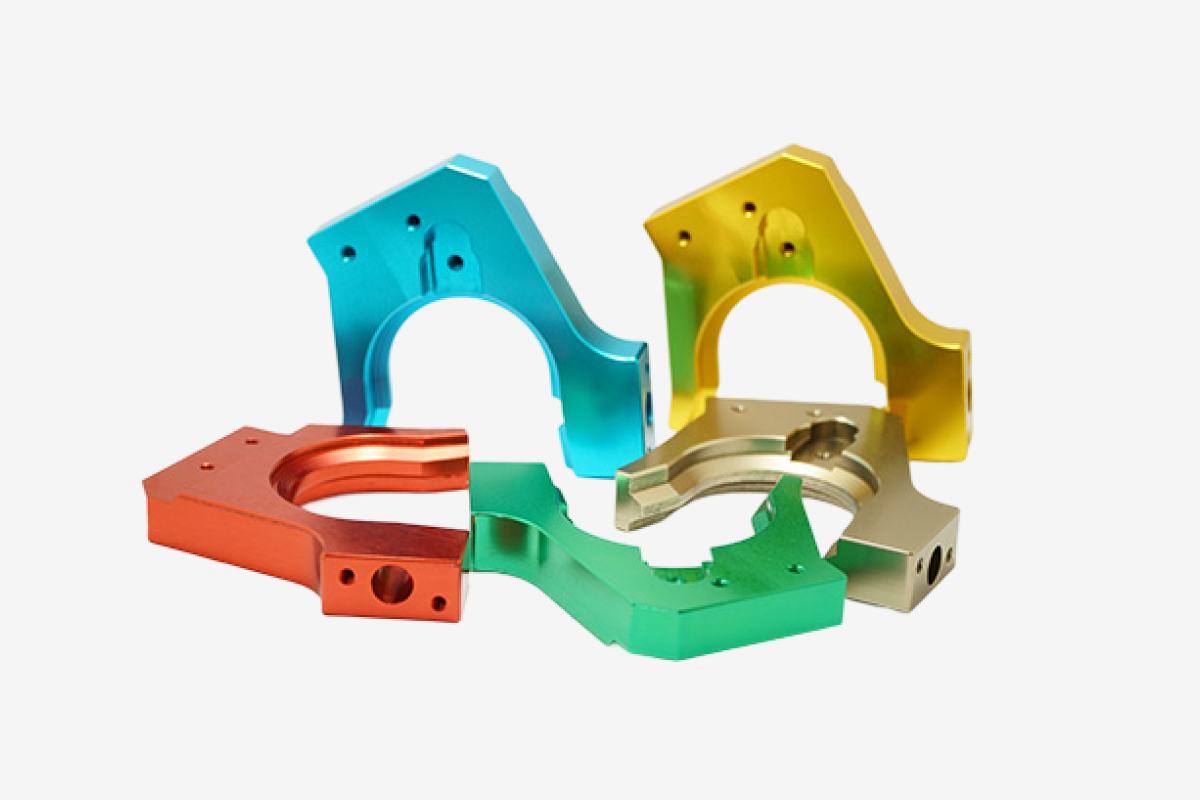
Colored Anodizing
Adds corrosion resistance and aesthetic appeal with various colors, commonly applied to aluminum parts.
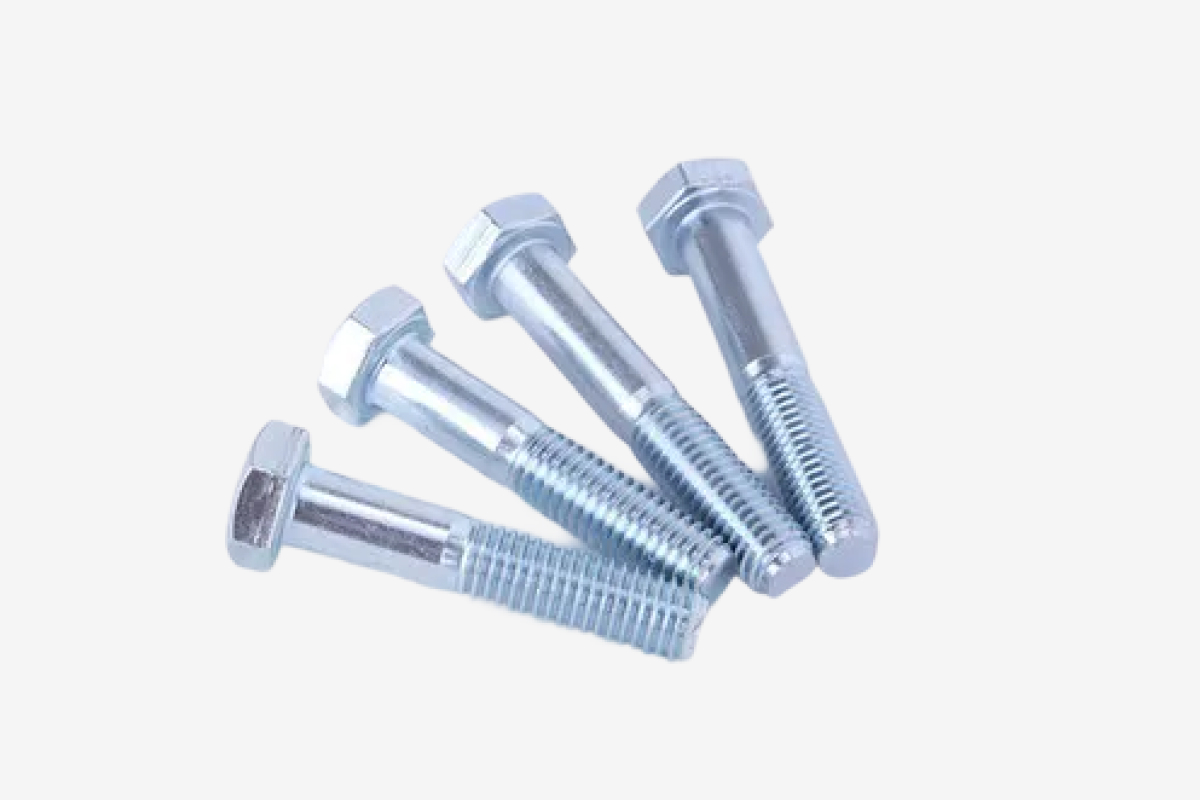
Zinc Plating
Protects steel from corrosion with a thin zinc layer, often used in automotive and construction.
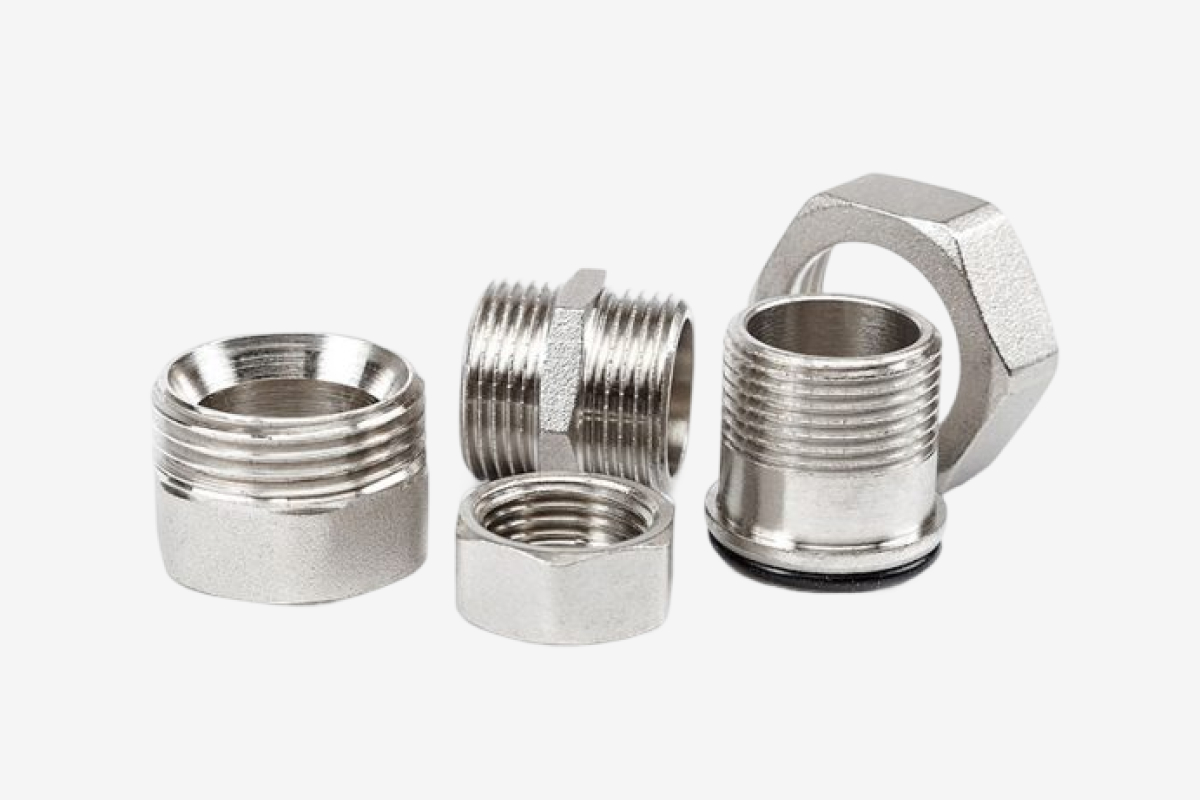
Nickel Plating
Improves wear resistance, hardness, and corrosion protection, widely used in mechanical and electronic components.
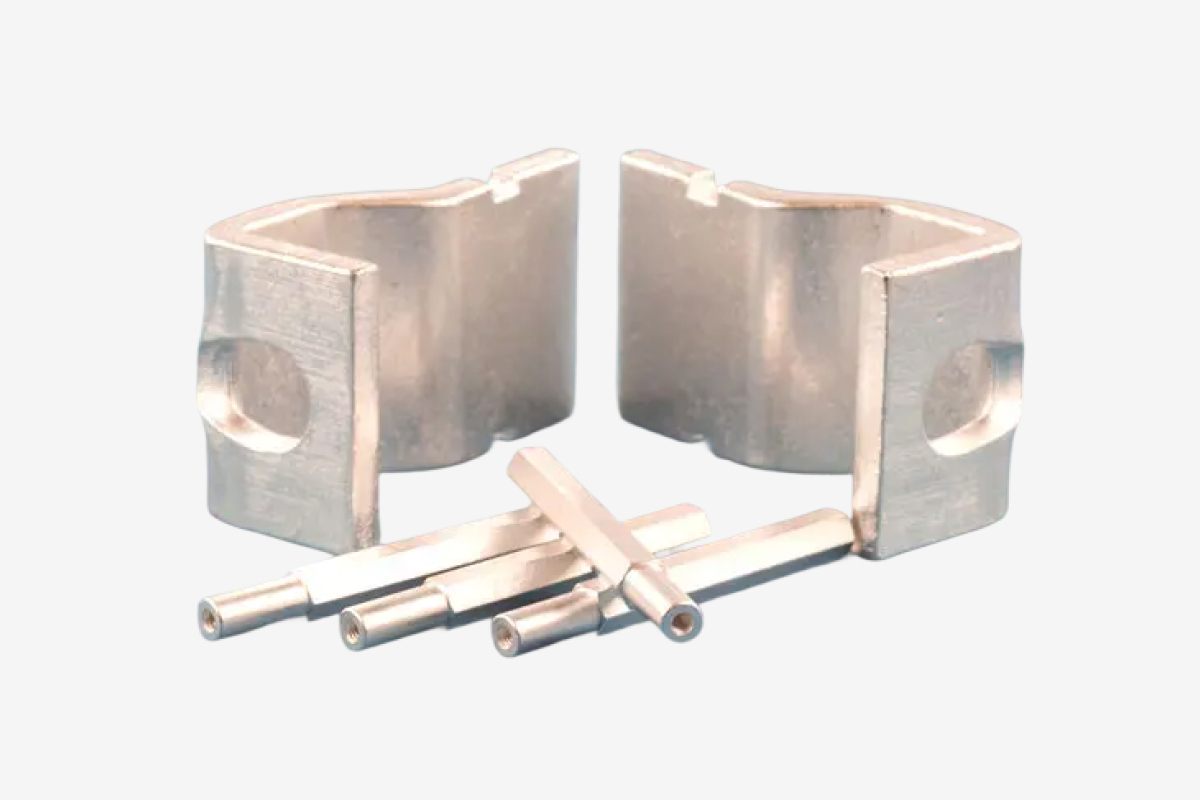
Tin Plating
Prevents oxidation, enhances solderability, and is commonly applied to electronic connectors.
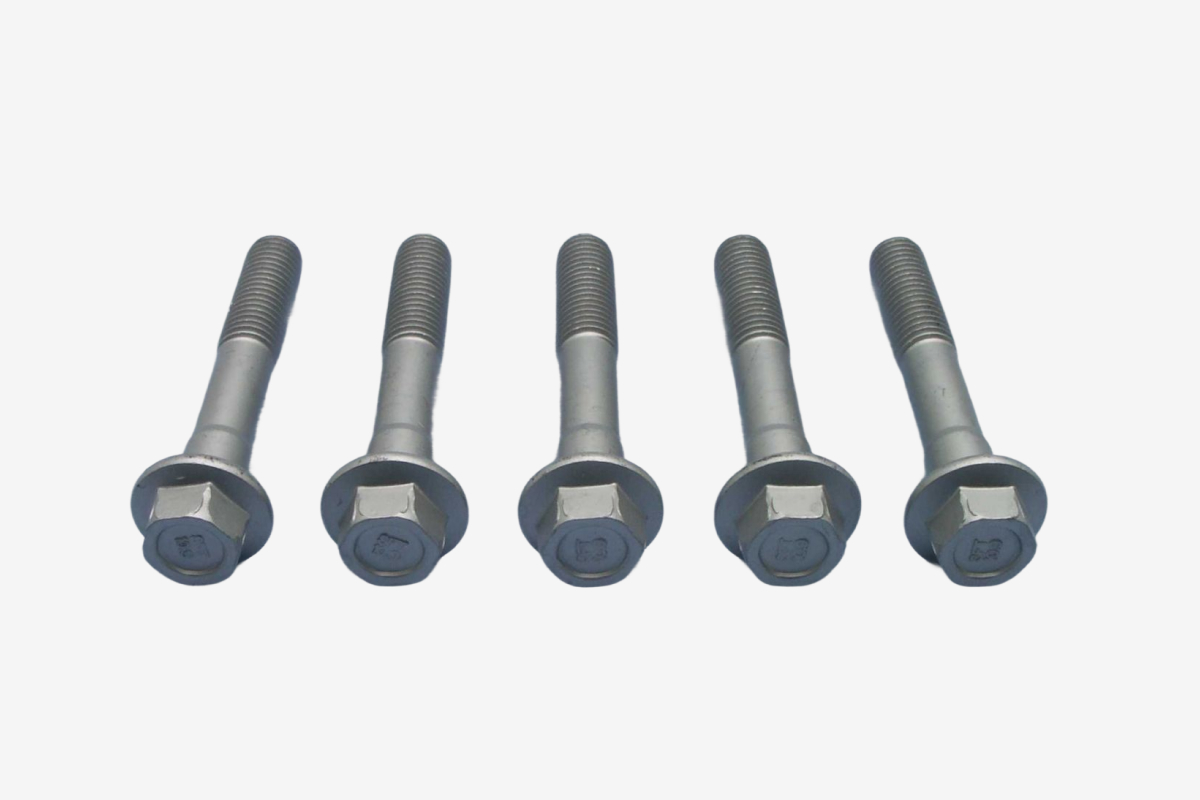
Zinc-Nickel Alloy Plating
Offers superior corrosion resistance and durability, widely used in automotive and aerospace industries.
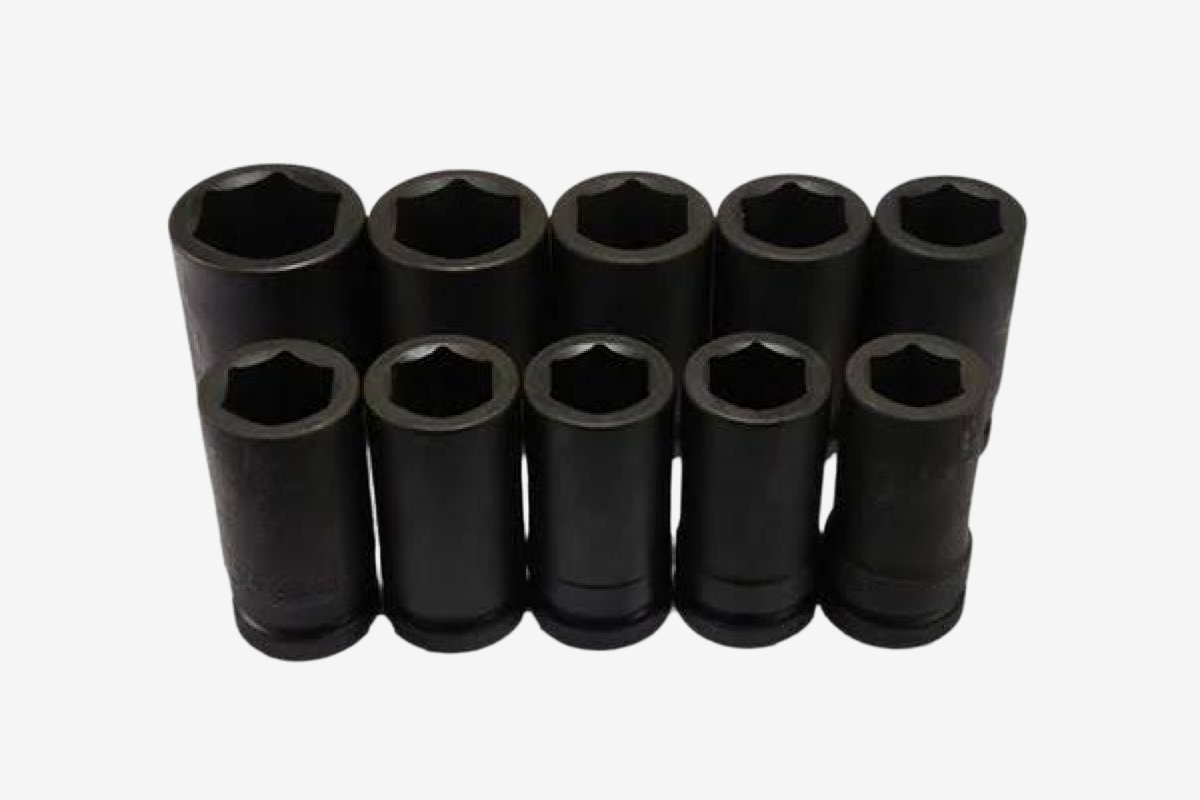
QPQ (Quench-Polish-Quench)
A surface hardening process that improves wear and corrosion resistance, used for precision components.
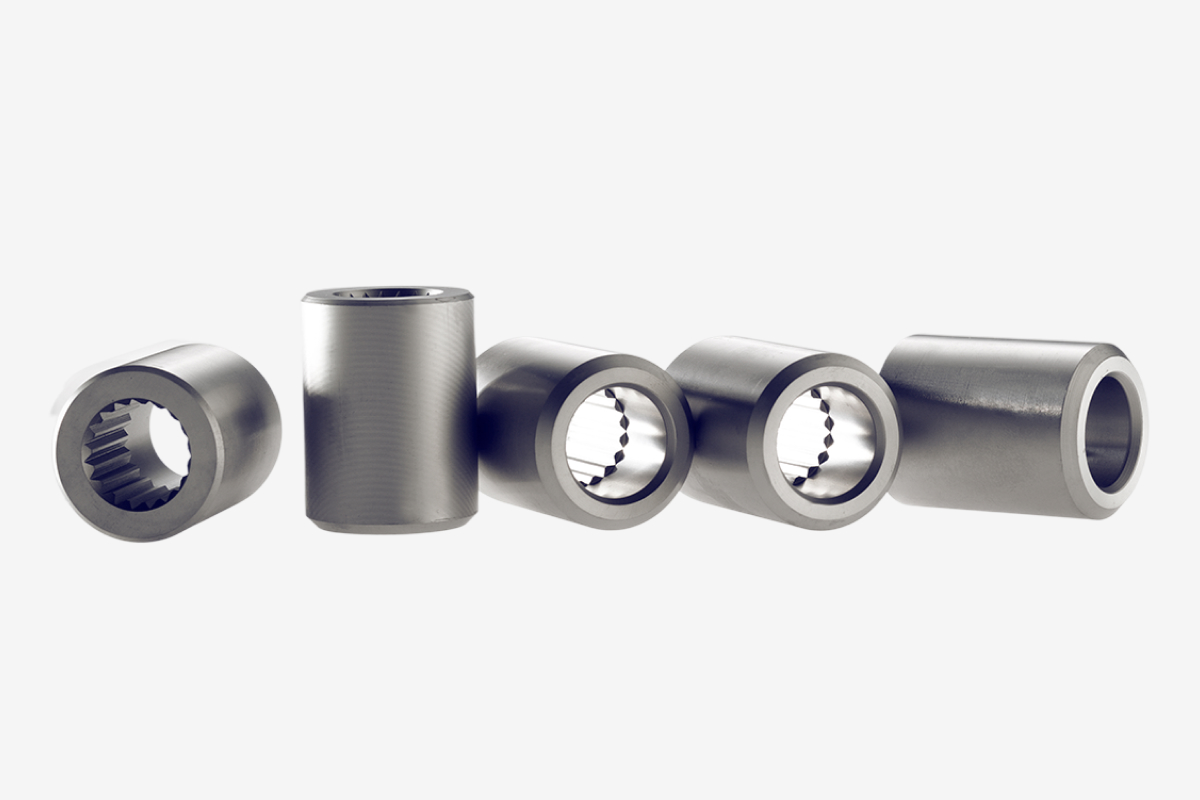
Plasma Nitriding
Enhances hardness and fatigue strength by diffusing nitrogen into the surface, ideal for high-performance applications.
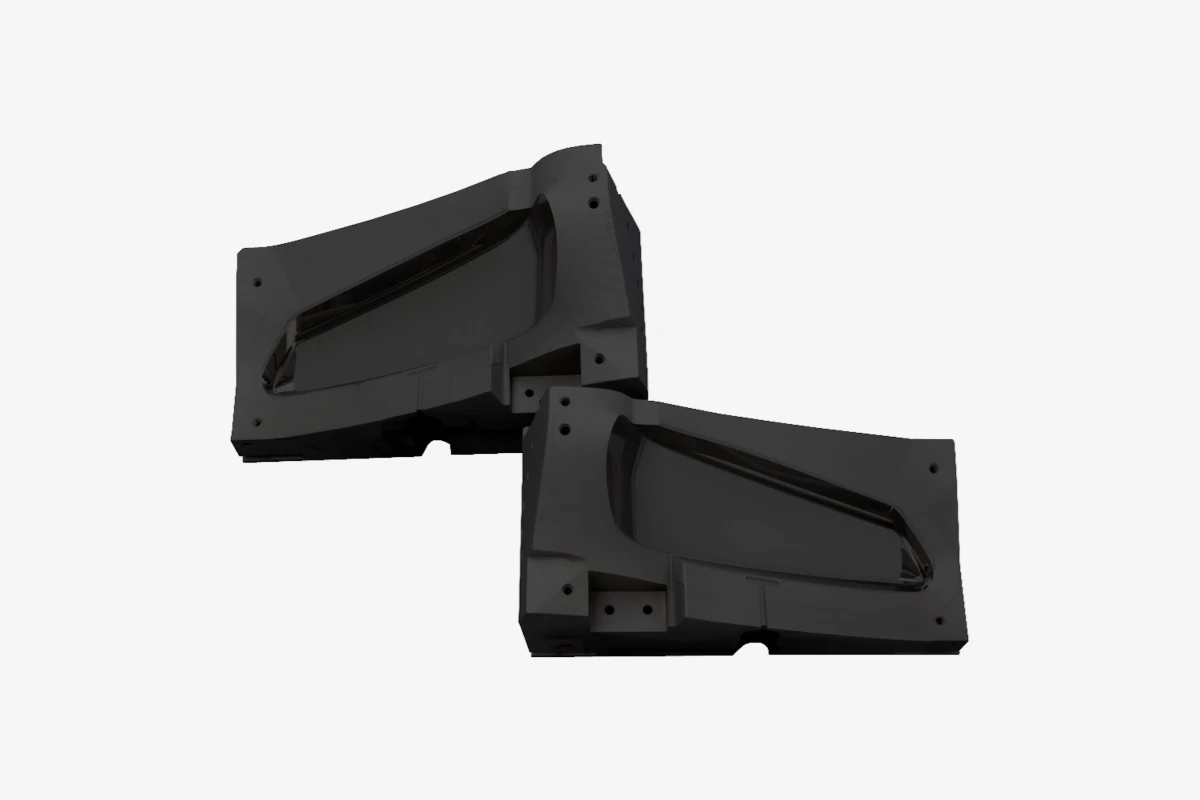
Spray Coating
Applies a protective or decorative paint layer to plastic surfaces, enhancing appearance, durability, and resistance to wear and chemicals.
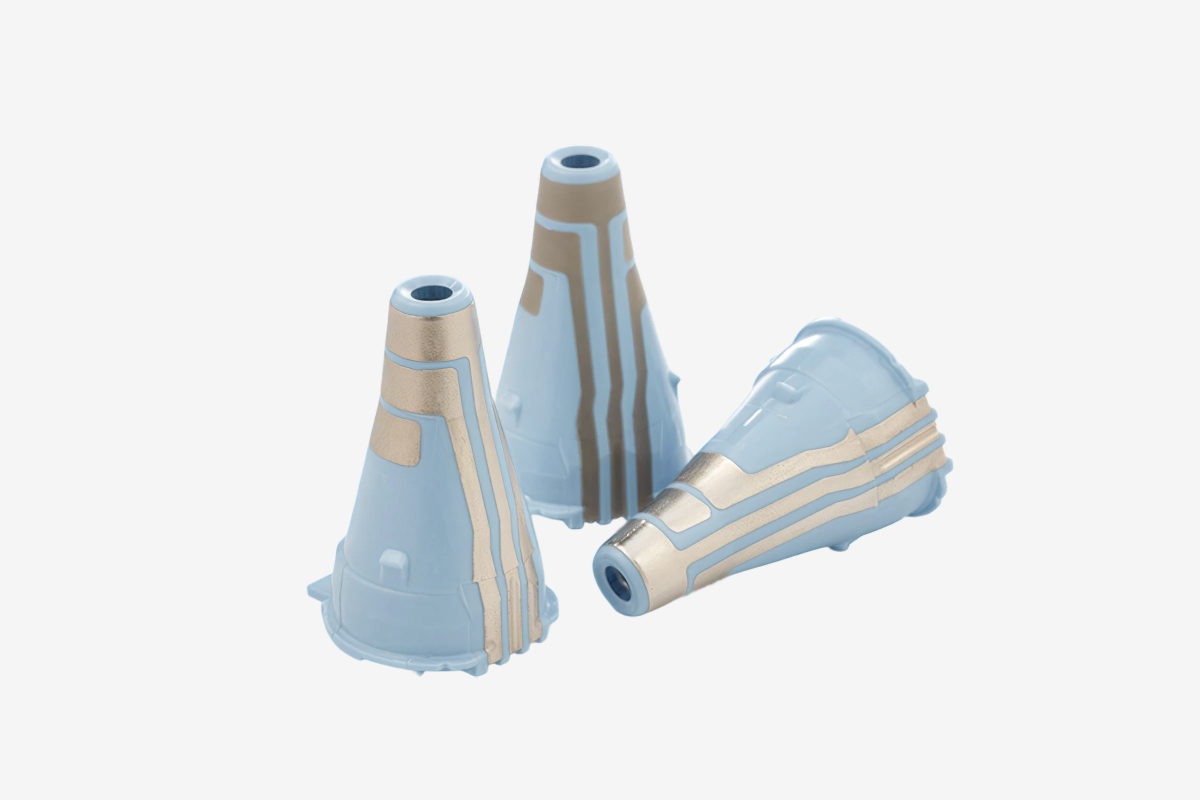
Water Plating
A surface treatment using electrolysis to deposit a thin metal layer on plastic parts, improving conductivity, corrosion resistance, and aesthetics.
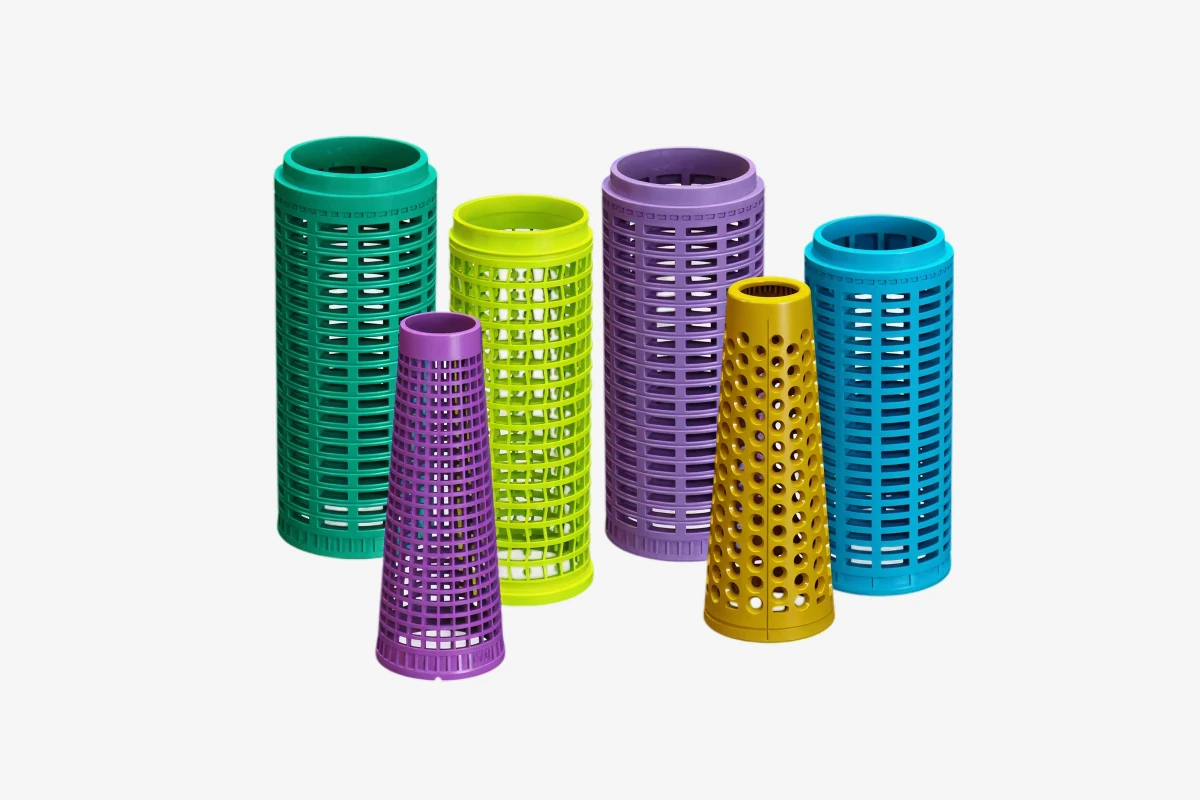
Color Dyeing
Infuses plastic with vibrant, lasting colors through a dyeing process, ensuring uniform appearance without affecting material properties.
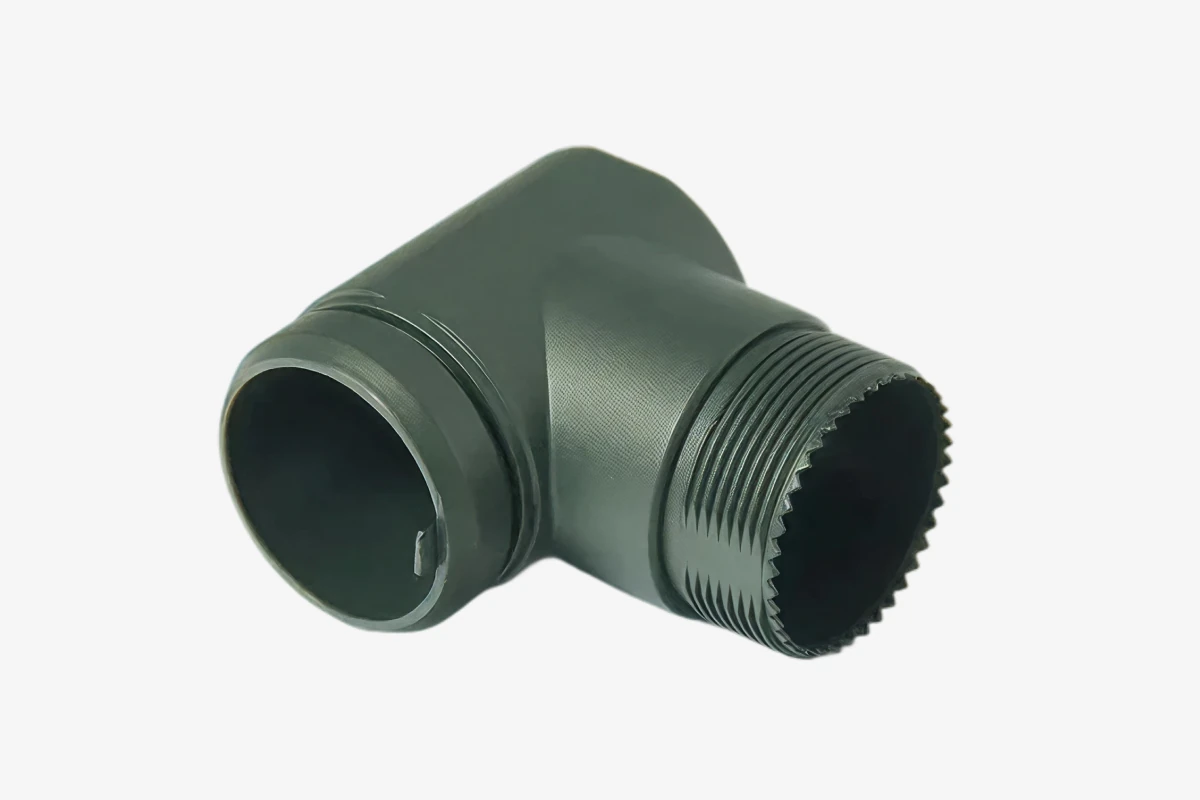
Sandblasting
Uses high-pressure abrasive particles to create a matte or textured finish on plastic surfaces, improving grip and aesthetics.
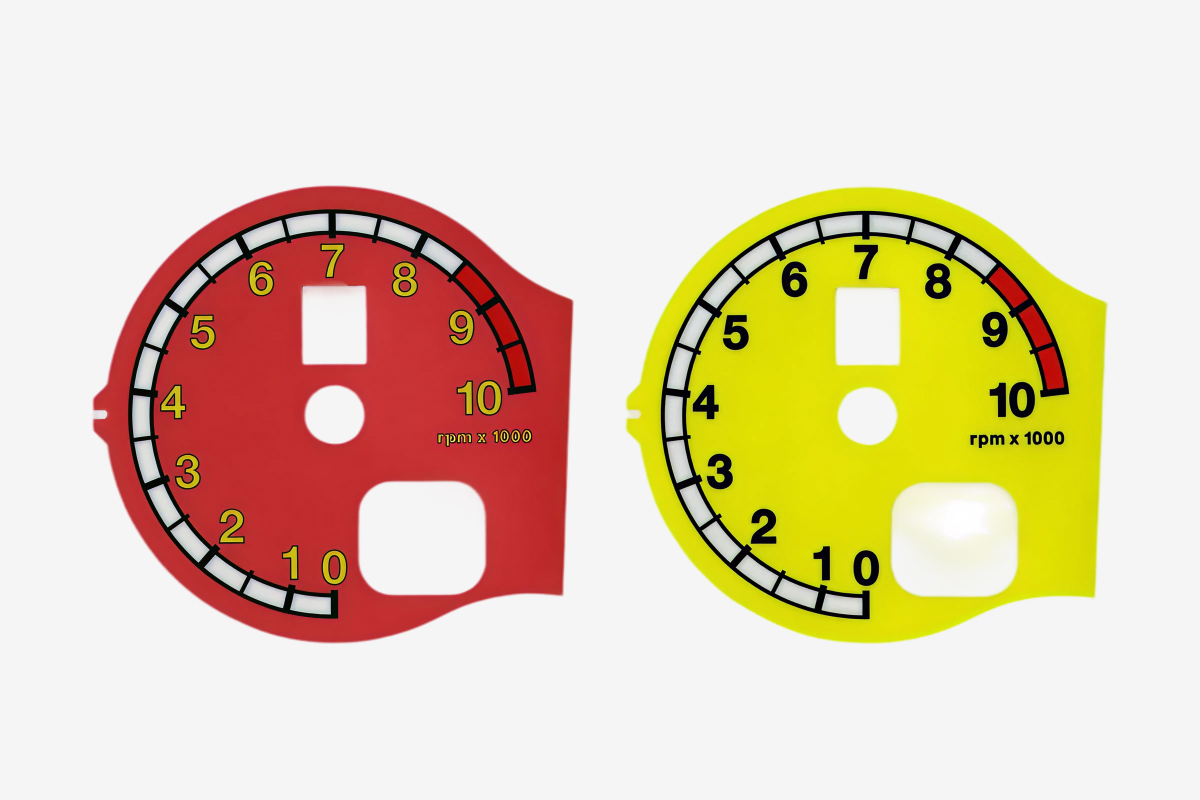
Silk Screening
Prints patterns, logos, or text on plastic parts using a mesh screen and ink, ensuring sharp, durable graphics.
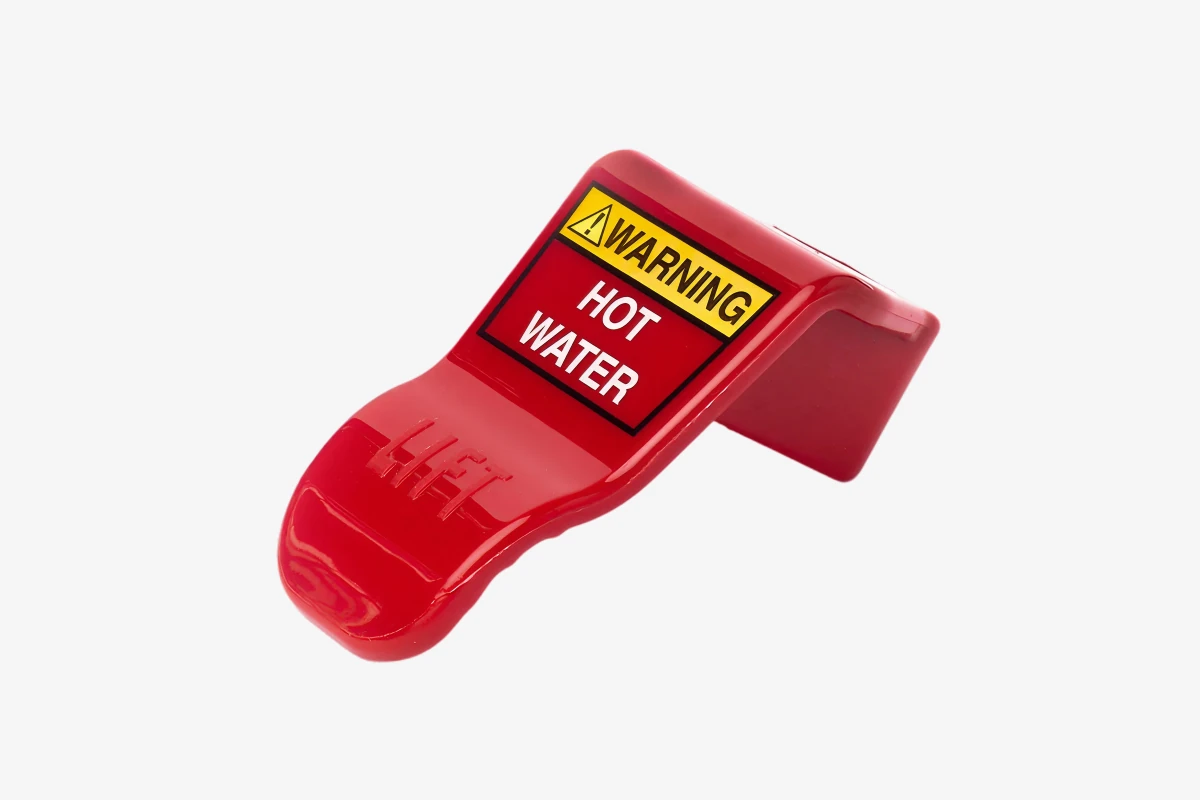
Pad Printing
Transfers ink from an engraved plate to plastic surfaces, ideal for detailed logos and multi-color designs.
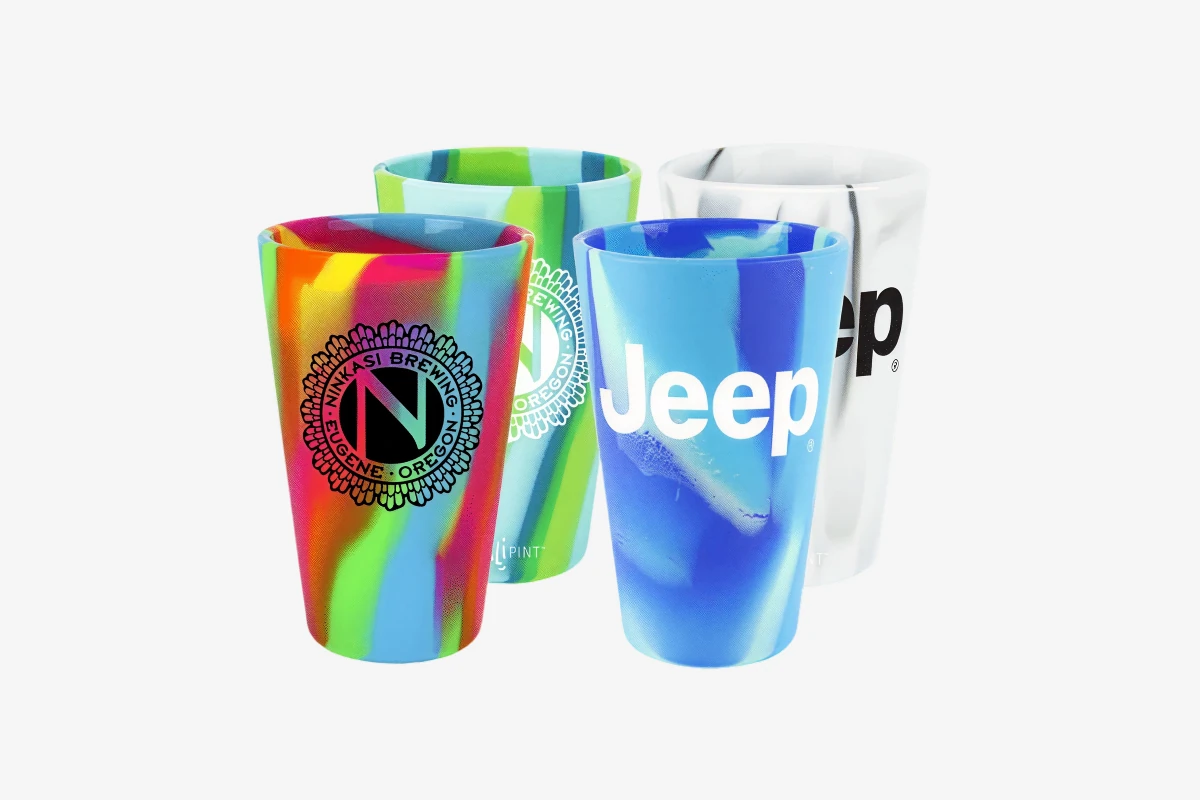
Water Transfer Printing
Uses a printed film on water to transfer intricate designs onto plastic parts, achieving a seamless decorative finish.
When it comes to surface finishing, selecting the right process is crucial for enhancing product quality and appearance. We offer a variety of surface finishing options for both metal and non-metal materials. Please refer to the following documents to explore the available surface finishing methods:
- Surface Finishing Options for Metal Materials, which provides detailed information on surface finishing techniques for metal parts.
- Surface Finishing Options for Non-metal Materials, covering various surface finishing methods for non-metal materials.
Surface Finishing Options for Metal Materials
No. | Material Finishing |
AL 2014 | AL 2017 | AL 5052 | AL 5080 | AL 5083 | AL 6061 | AL 6063 | AL 6082 | AL 7050 | AL 7075 | Mg | Brass | Red Copper | Bronze | Stainless Steel | M303E | A3 Steel | 45# Steel | AZ91D | AZ91B | ZN |
1 | Plastic Painting (done in house) | √ | √ | √ | √ | √ | √ | √ | √ | √ | √ | √ | √ | √ | √ | √ | √ | √ | √ | √ | √ | |
2 | Metallic Painting (done in house) | √ | √ | √ | √ | √ | √ | √ | √ | √ | √ | √ | √ | √ | √ | √ | √ | √ | √ | √ | √ | |
3 | Rubber Oil Painting (done in house) | √ | √ | √ | √ | √ | √ | √ | √ | √ | √ | √ | √ | √ | √ | √ | √ | √ | √ | √ | √ | |
4 | UV Oil Painting (done in house) | √ | √ | √ | √ | √ | √ | √ | √ | √ | √ | √ | √ | √ | √ | √ | √ | √ | √ | √ | √ | |
5 | Plating (subcontract) | √ | √ | √ | √ | √ | ||||||||||||||||
6 | Brushing (subcontract) | √ | √ | √ | √ | √ | √ | √ | √ | √ | √ | √ | √ | |||||||||
7 | Smooth (done in house) | √ | √ | √ | √ | √ | √ | √ | √ | √ | √ | √ | √ | √ | √ | √ | √ | √ | √ | √ | √ | √ |
8 | Polishing (done in house) | √ | √ | √ | √ | √ | √ | √ | √ | √ | √ | √ | √ | √ | √ | √ | √ | √ | √ | √ | √ | √ |
9 | Mirror Polishing (done in house) | √ | √ | √ | √ | √ | √ | √ | √ | √ | √ | √ | √ | √ | √ | √ | √ | √ | √ | √ | √ | √ |
10 | Silk-Screen (done in house) | √ | √ | √ | √ | √ | √ | √ | √ | √ | √ | √ | √ | √ | √ | √ | √ | √ | √ | |||
11 | Sandblasting (done in house) | √ | √ | √ | √ | √ | √ | √ | √ | √ | √ | √ | √ | √ | √ | √ | √ | √ | ||||
12 | Clear and Color Anodizing (subcontract) | √ | √ | √ |
Why Choose Us
Expertise for Flawless Results
With years of experience, we provide precise surface finishing that enhances part quality.
Wide Range of Finishing Options
We offer various surface treatments to meet your specific needs, ensuring the best results.
Fast Turnaround, Efficient Service
Our streamlined processes ensure on-time delivery, speeding up your project timeline.
Strict Quality Control
Every part undergoes thorough inspection to guarantee the highest standards of surface finish.
FAQs about Surface Finishing
Surface finishing is a set of technique for altering the surface of a workpiece for the improvement of its functions or appearance. Example of surface finishing include painting, annealing, or anodizing.
The industry standard for surface finish is surface roughness measured by roughness average (Ra).
Different industries have their surface roughness requirements
Common types of surface finishes available at GS Proto include:
- Polishing
- Anodizing
- Plating
- Sandblasting
- Painting
Choosing any of the above depends on your project requirement, available finish, and the budget.
The surface finish is calculated using a profilometer which measures the workpiece surface roughness in micrometers or microns.
The surface finish of a product depends on the following:
- Manufacturing process
- Material type
- Tool quality
- Speed of production
Surface finish can help improve a part’s functionality or its aesthetics. For example, anodizing improves surface hardness and offer many color options while painting offers more of corrosion resistance and color options.
Use surface finishing process such as polishing or lapping to get a mirror like surface finish
Before you choose a surface finish technique, you must consider the part’s intended use, the type of material, whether you need functional, aesthetics, or both improvement.
Your budget and the industry requirement will also shape your choice. Contact us at GS Proto to guide you on making the right choice
Yes, some surface finishing methods can have environmental impacts. Techniques like plating and anodizing can produce toxic chemicals or waste which can impact the environment
Regardless, GS Proto complies with all environmental standards to minimize negative impacts.
Lead time for surface finishing services depends on the technique you use. Painting can be as fast as a two days while techniques like electroplating can take longer.
The driving force for the lead time of using a surface finishing option is the technique, part dimension, order size, and capability of the surface finishing service.
Lead time ranges from a few days to a couple of weeks
Start With a Free Project Review
Ready to enhance your parts with superior surface finishes? Contact us today to get started on your project!
Laets Blog
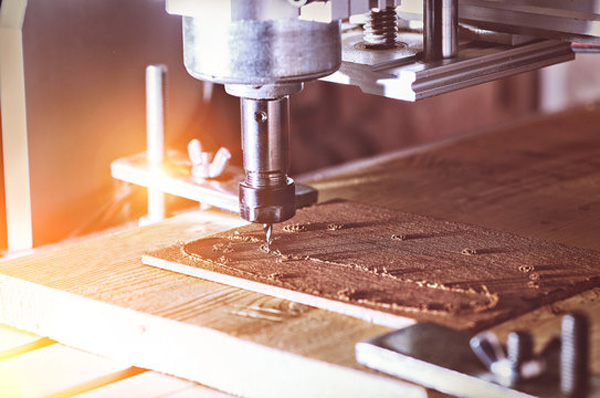
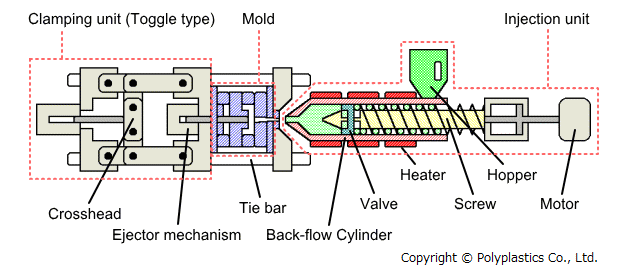