Wire EDM Machining Services
GS Proto has over 10 years of EDM expertise, producing precise and intricate wire-cut parts—ideal for complex geometries requiring the highest standards.
- High Precision Cutting
- No Thermal Distortion
- Versatile for Any Material
Precision Wire EDM Solutions by GS Proto
Wire EDM is a high-precision cutting process using electrical discharge and a fine wire to create complex parts with smooth, stress-free finishes. GS Proto delivers fast, top-quality wire-cut components with decades of expertise and an extensive workshop network.
- Rapid Turnaround – Delivering precision parts in days, not months.
- Exceptional Accuracy – Achieves tight tolerances with no need for post-processing.
- Versatile Manufacturing – Capable of handling both simple and highly intricate designs.
- Certified Excellence – Our facilities meet ISO 9001, 13485, 14001, IATF 16949, and D-U-N-S® standards.
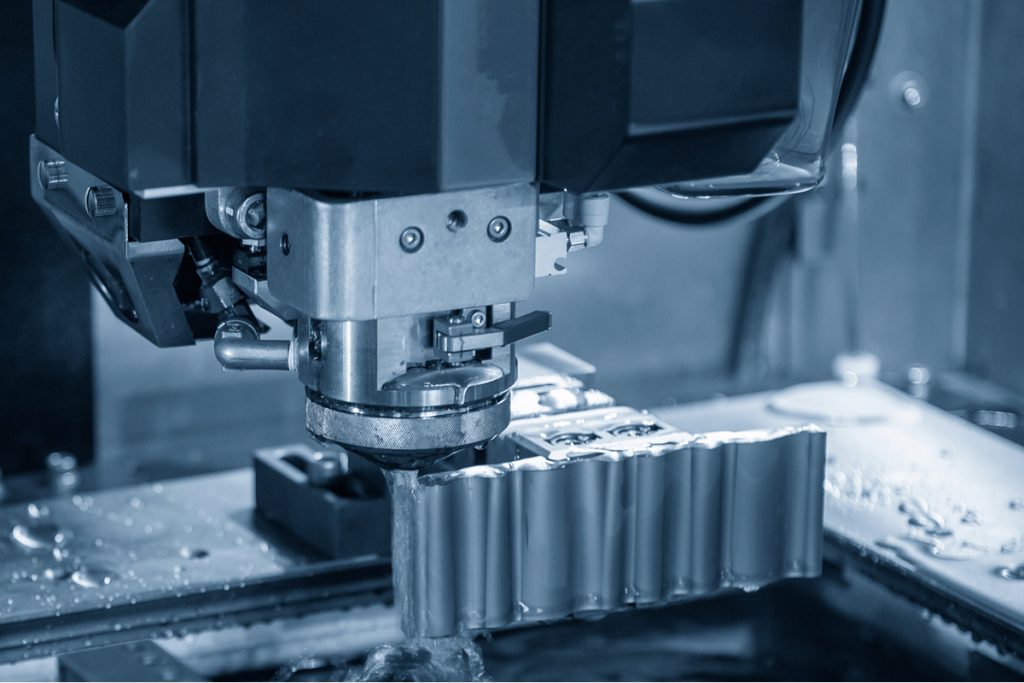
Why Choose Us
High-Precision Parts
Advanced EDM machines achieve tolerances up to ±0.001” for high-accuracy components.
Fast Delivery
GS Proto ensures rapid production, completing projects in as little as one day without sacrificing quality.
Cost Savings
High-precision results at lower costs than traditional machining.
Expert Support
Our skilled engineers provide guidance from design to production for the optimized parts.
Wire EDM Parts Gallery
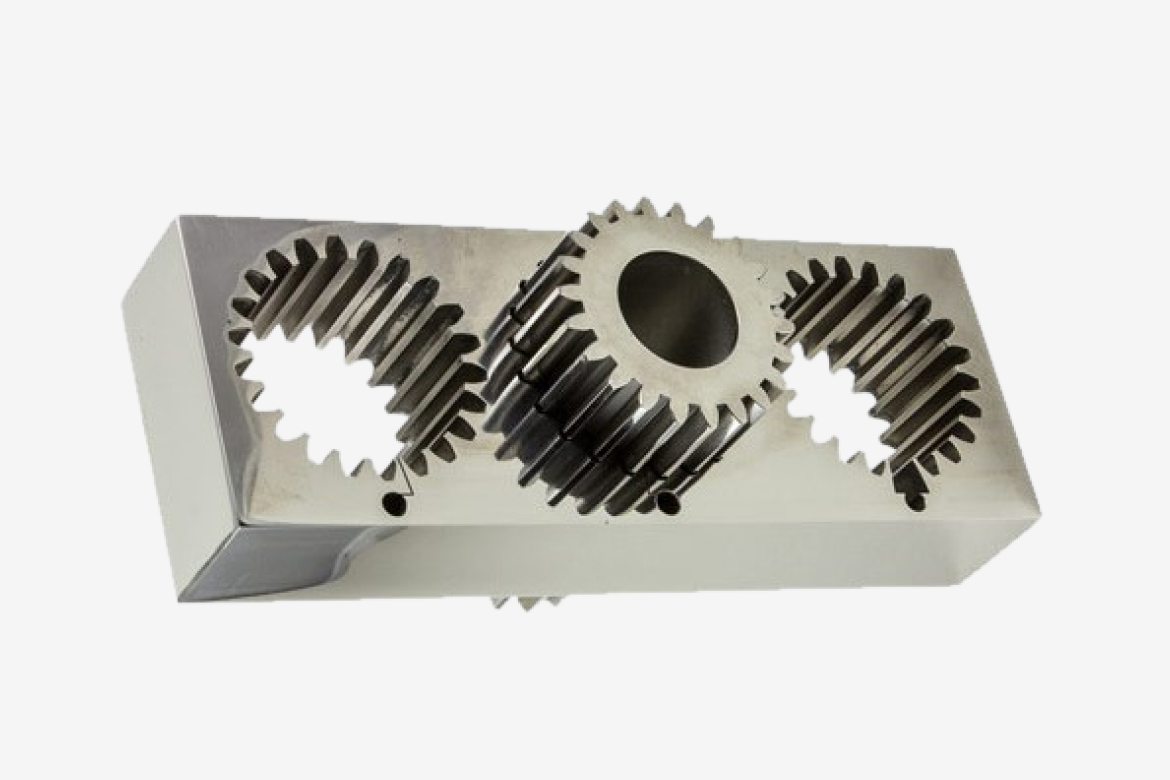
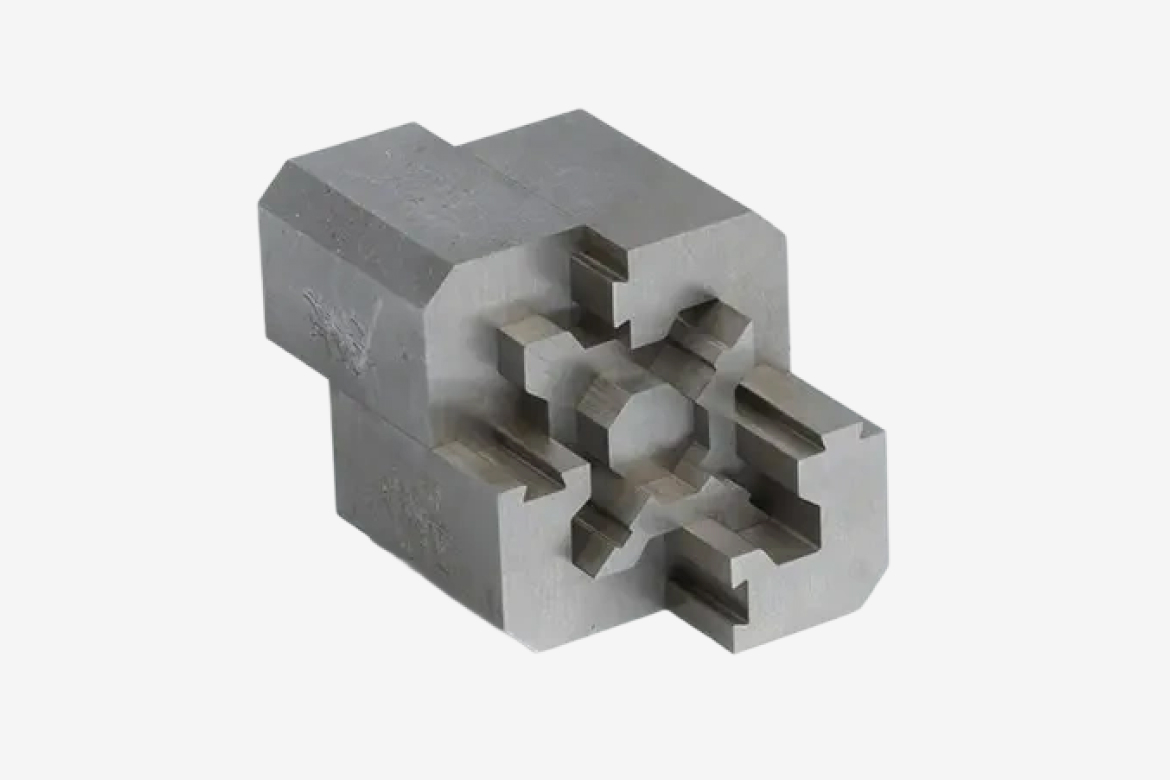
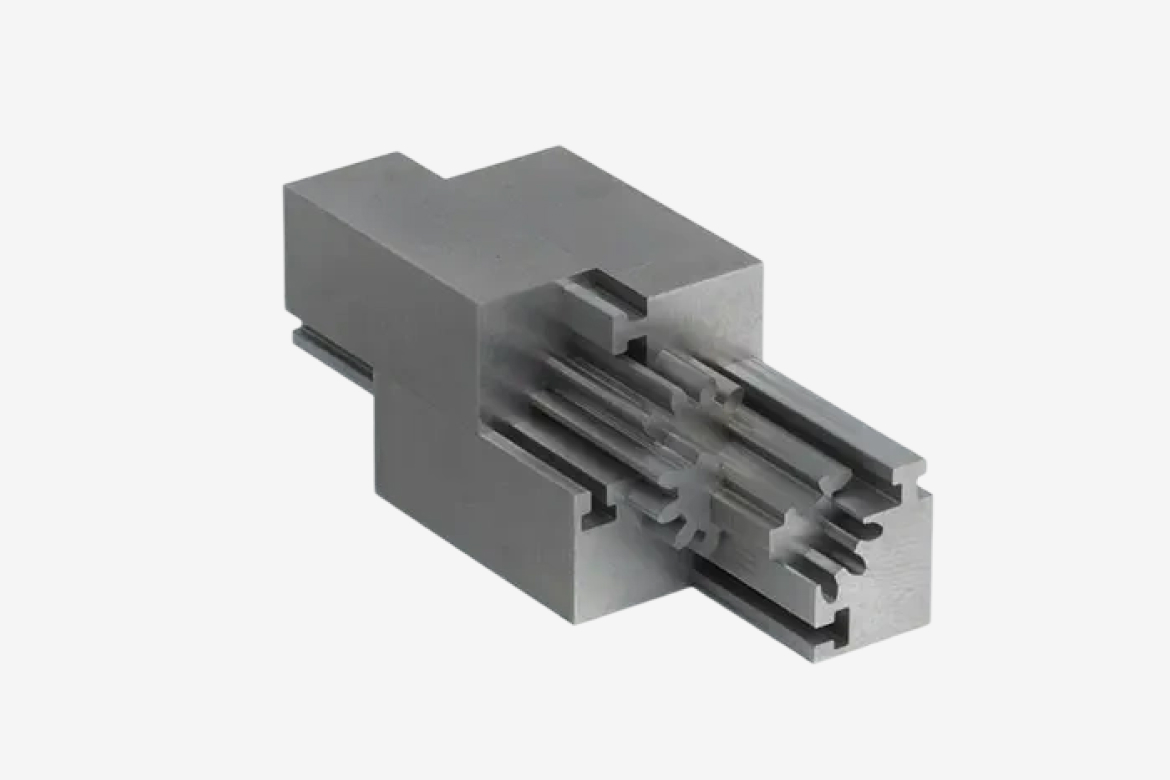
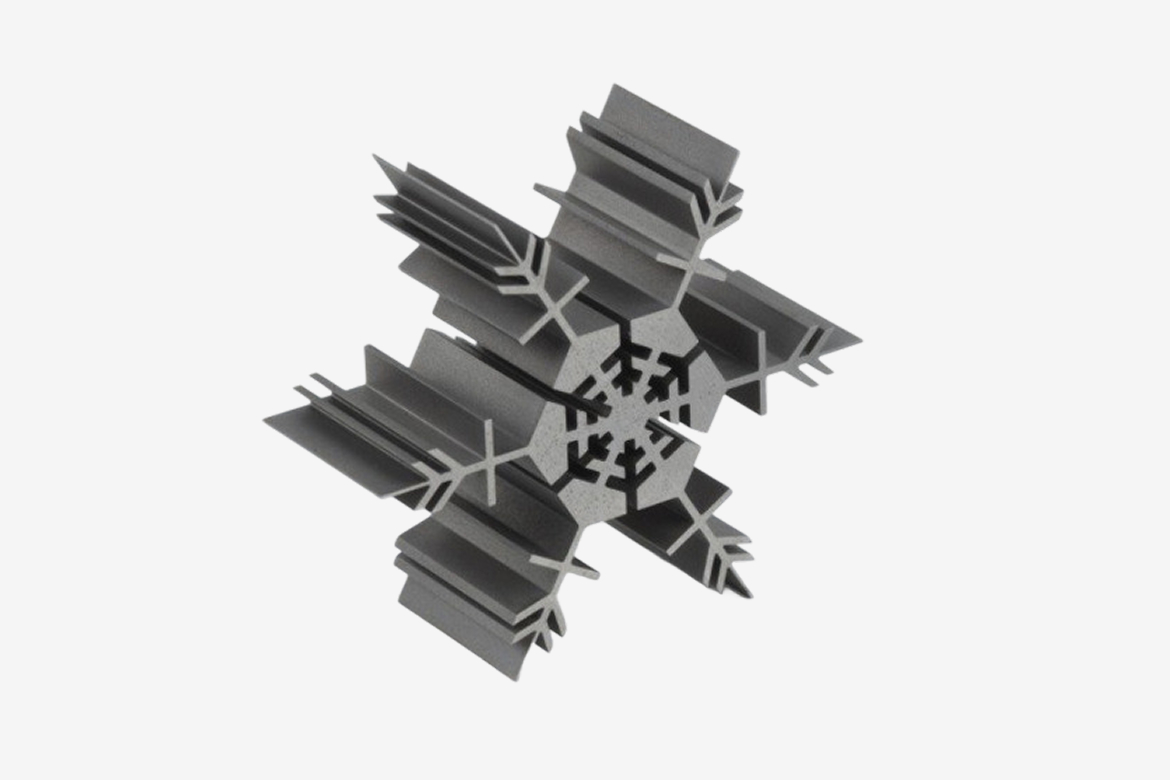
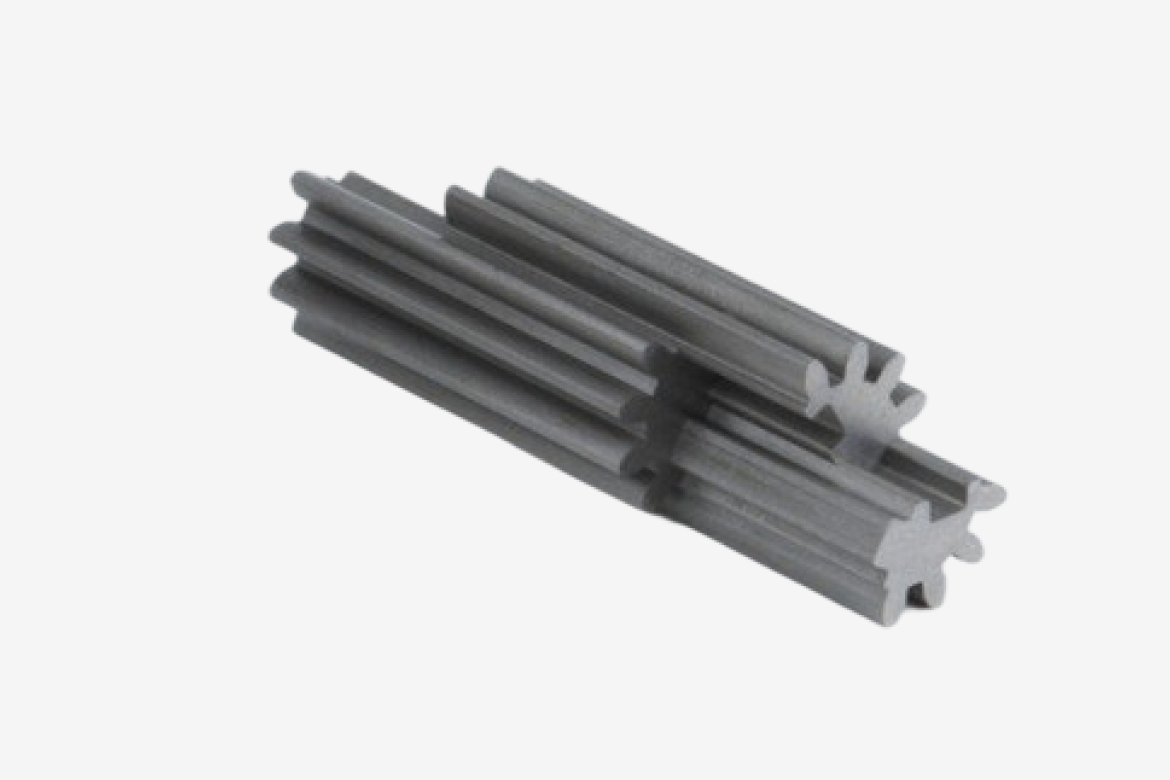
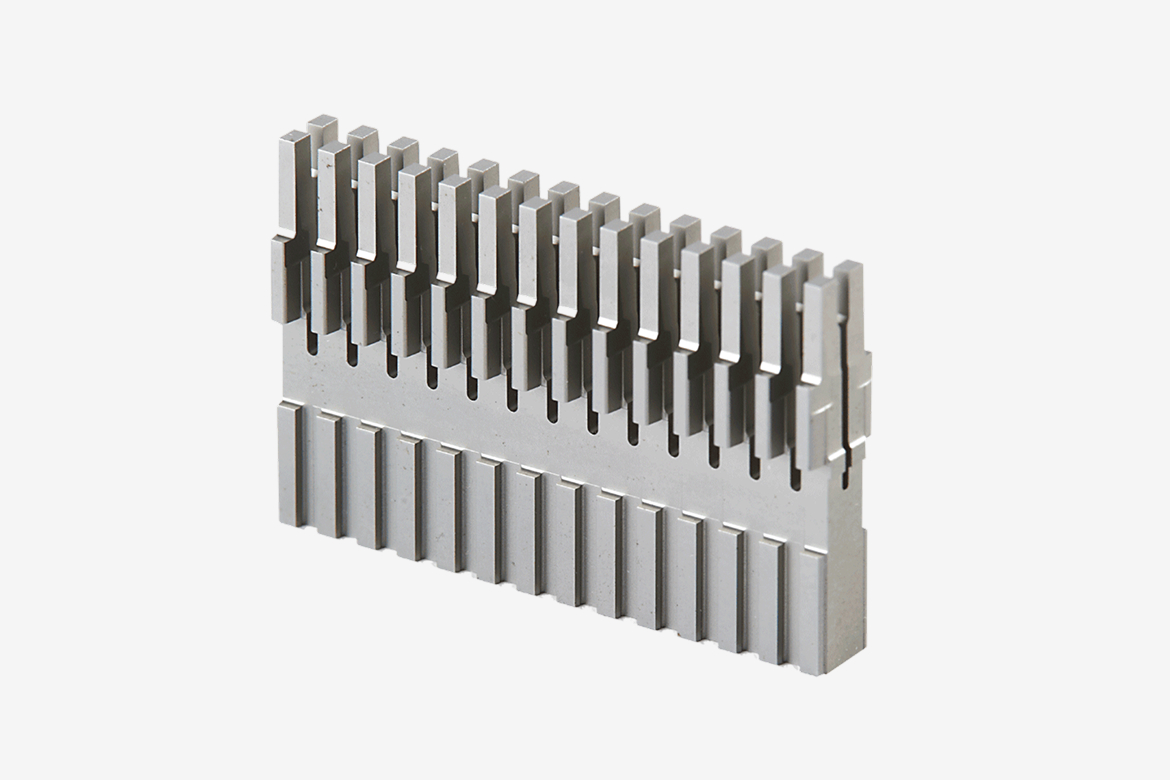
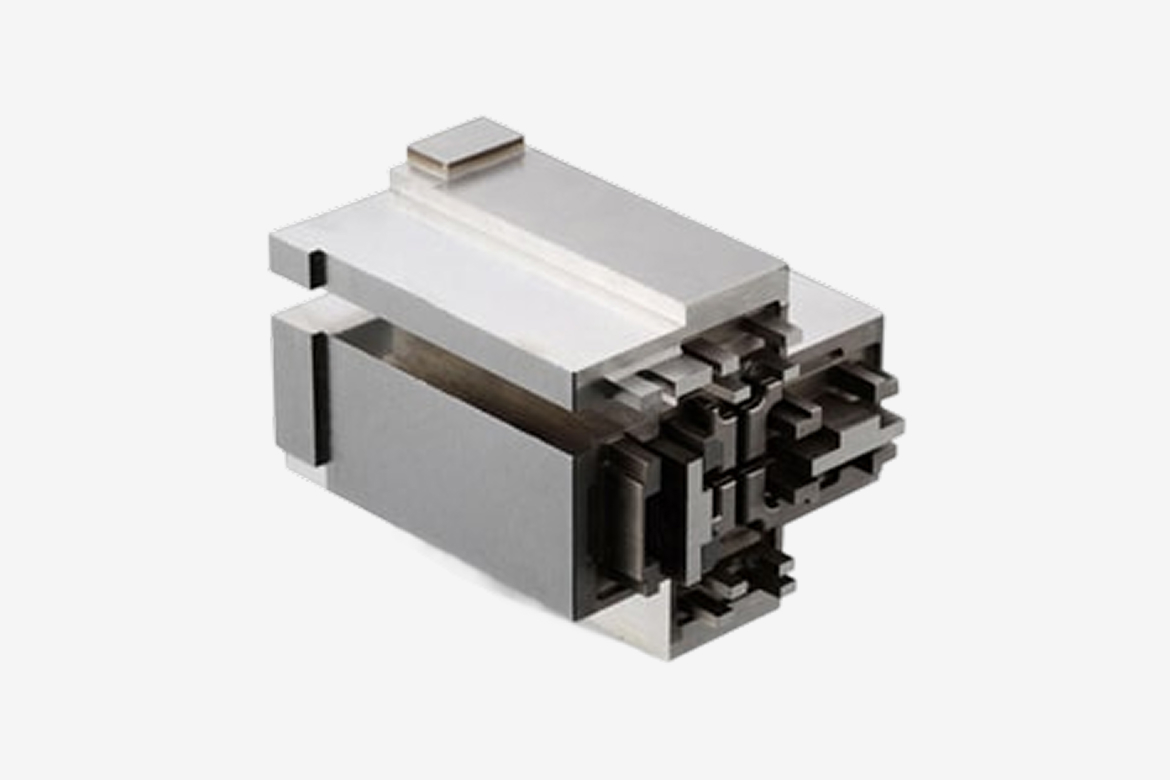
Wire EDM Materials
GS Proto’s Wire EDM services expertly machine various conductive materials, including superalloys and hardened steels, delivering precise and durable parts for high-demand industries.
Metals
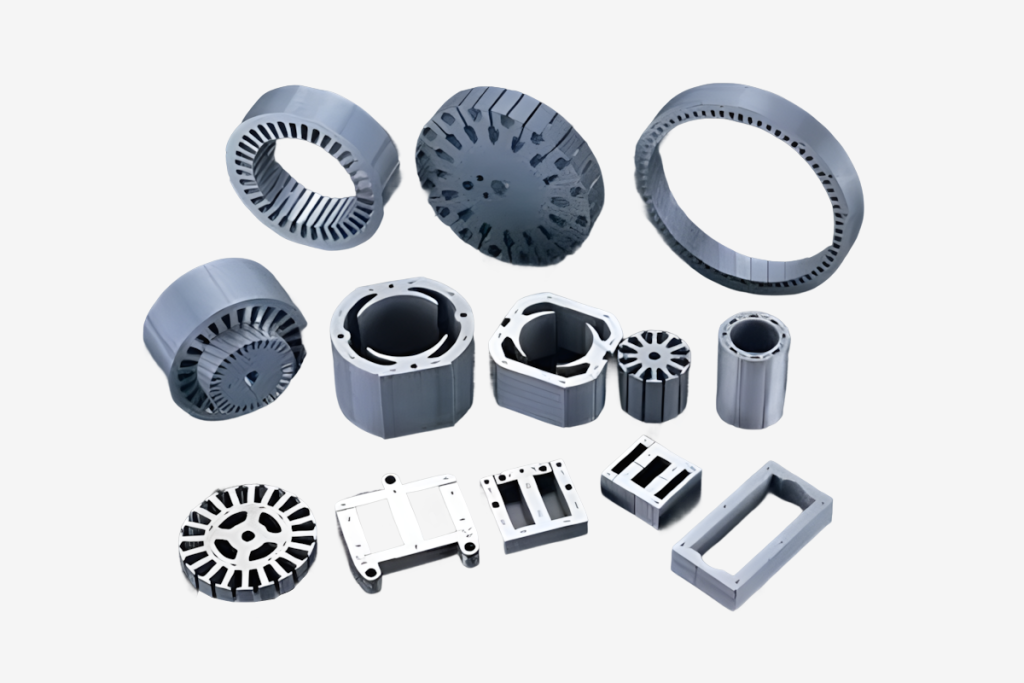
Stainless steel provides exceptional corrosion resistance and strength, making it perfect for durable, long-lasting components in industries like medical and food processing.
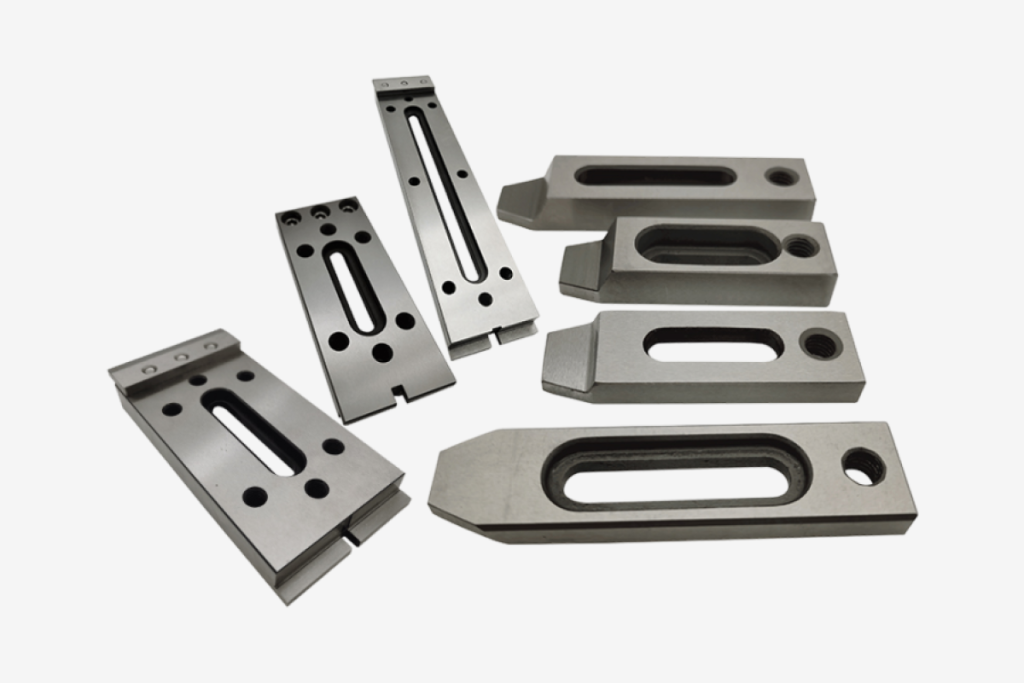
Titanium offers a remarkable strength-to-weight ratio and is biocompatible, making it ideal for aerospace and medical implants that demand both durability and lightweight characteristics.
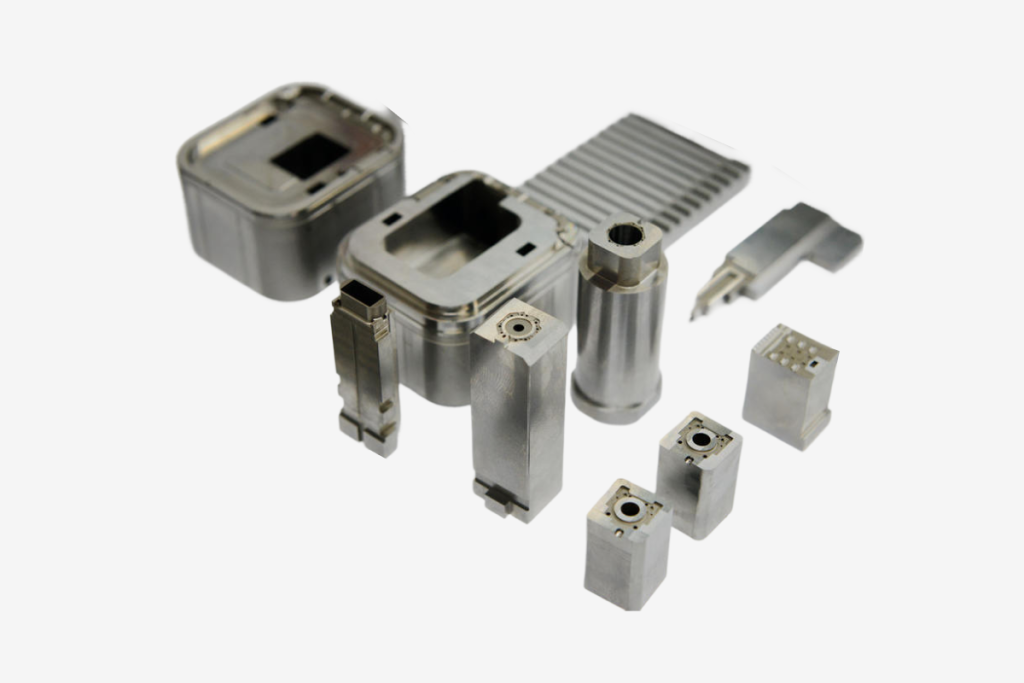
Aluminum is lightweight, easy to machine, and offers excellent corrosion resistance and electrical conductivity, making it a popular choice in aerospace, automotive, and electronics industries.
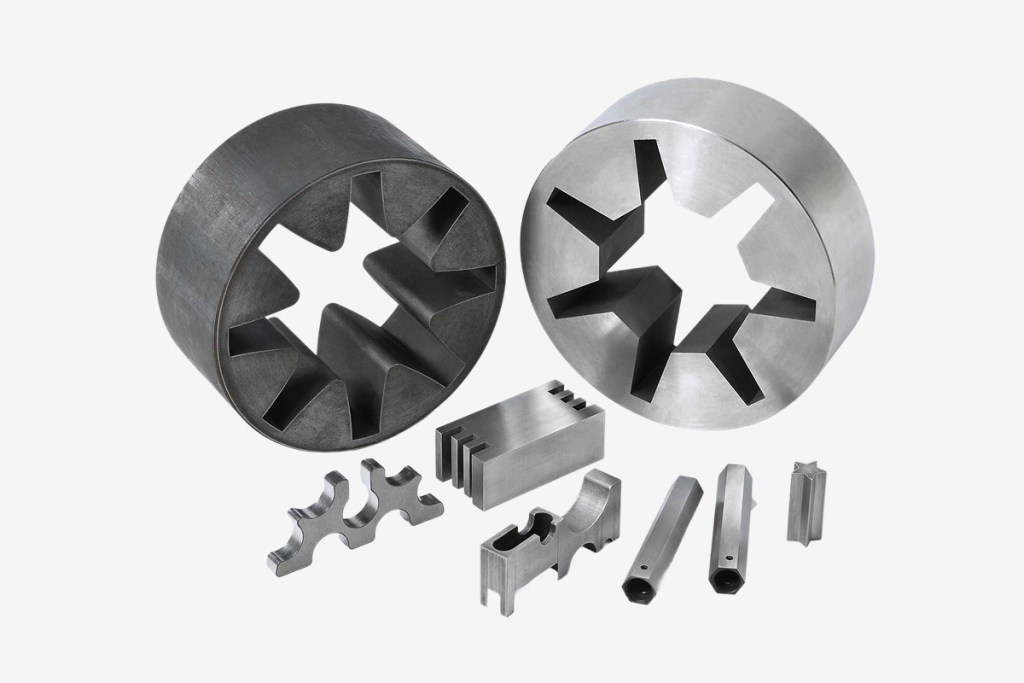
Steel and hard tool steel are prized for their toughness and wear resistance, making them ideal for high-stress applications like cutting tools, molds, and heavy machinery components.
Wire EDM Materials
Lorem ipsum dolor sit amet, consectetur adipiscing elit. Ut elit tellus, luctus nec ullamcorper mattis, pulvinar dapibus leo.
Lorem ipsum dolor sit amet, consectetur adipiscing elit. Ut elit tellus, luctus nec ullamcorper mattis, pulvinar dapibus leo.
Lorem ipsum dolor sit amet, consectetur adipiscing elit. Ut elit tellus, luctus nec ullamcorper mattis, pulvinar dapibus leo.
Wire EDM Part Size Standards
GS Proto can handle diverse part sizes machined by wire EDM, from intricate micro components to larger, complex assemblies, ensuring precise adherence to dimensional standards.
Small Parts (mm) | Medium Parts (mm) | Large Parts (mm) | |
---|---|---|---|
Maximum Length | 50 | 100 | 500 |
Maximum Width | 30 | 70 | 300 |
Maximum Height | 10 | 40 | 150 |
Minimum Thickness | 0.5 | 1.0 | 5.0 |
Tolerance | ±0.005 | ±0.01 | ±0.03 |
Our Precision Wire EDM Machining
Achieve ultra-fine cuts with high accuracy. Upload your design today!
Advantages and Applications
Advantages of Wire EDM Machining
-
Precision:
Achieves tight tolerances (up to +/- 0.0001 inches) for high-demand industries. -
Complex Shapes:
Creates intricate geometries impossible with traditional methods. -
Material Flexibility:
Cuts all conductive materials, including tough metals, without distortion. -
Smooth Finishes:
Provides near-finish-quality surfaces, reducing post-processing. -
No Contact Cutting:
Eliminates mechanical stress, ideal for delicate parts.
Applications of Wire Cut Parts
-
Aerospace:
Manufactures high-precision, complex parts for performance-critical applications. -
Medical Devices:
Produces intricate, reliable implants and surgical tools. -
Tool & Die Making:
Ideal for detailed molds, dies, and fixtures with tight tolerances. -
Automotive:
Enables production of precision gears and key components with exacting standards. -
Custom Manufacturing:
Supports bespoke solutions for specialized machinery and exotic materials.
How to Work with GS Proto
Working with GS Proto is simple and efficient. Just upload your CAD files and product details, and our expert team will handle the rest, ensuring precision, fast turnaround, and top-quality results for your wire EDM projects.
Get High-Quality Wire EDM Services
Get complex, tight-tolerance parts with smooth finishes. Start your project now!
FAQs
Yes, GS Proto’s Wire EDM can precisely cut materials up to 12 inches (300 mm) thick. The process efficiently erodes dense materials without distortion, making it ideal for heavy-duty parts like aerospace components and molds.
Wire EDM has a few limitations:
- It only works on electrically conductive materials.
- Cutting speed is slower than some traditional methods, especially for thick materials.
- Operational costs, including wire and fluid supply, can be higher.
- Setup and programming require skilled operators.
- Achieving the highest surface finishes may require additional passes.
Wire EDM creates intricate 2D and 3D shapes, including sharp internal corners, complex contours, and narrow slots. It excels in precision for aerospace, medical, and mold-making applications.
For standard applications, Wire EDM achieves tolerances ranging from ± 0.005 to ± 0.03 mm, depending on part size and complexity. In specialized cases, it can reach precision as tight as ±0.0001 inches (±2.5 microns). This capability allows for the creation of complex shapes and smooth surfaces, making it ideal for high-precision industries like aerospace and medical devices.
- Wire EDM: Cuts intricate shapes in conductive materials with high precision.
- Sinker EDM: Uses custom electrodes for detailed cavities and shapes.
- Hole-Drilling EDM: Specializes in precise holes, often for turbine blades or as prep for Wire EDM.
Yes, Wire EDM efficiently machines hard materials like hardened tool steels, titanium, and superalloys. It avoids tool wear and material distortion, ensuring precision and high-quality finishes.
Latest Blog
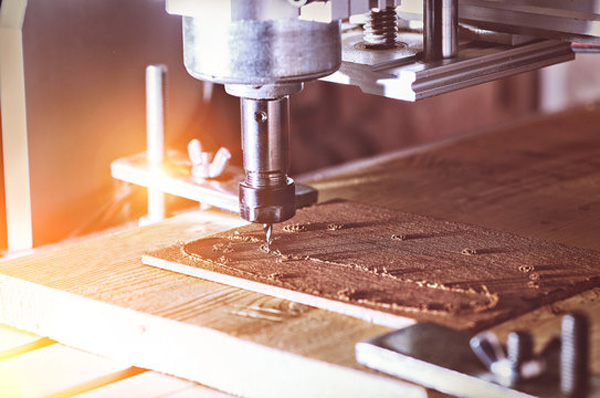
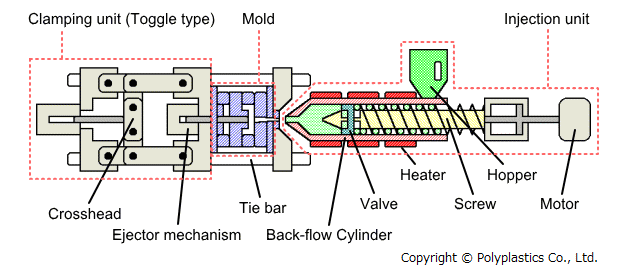